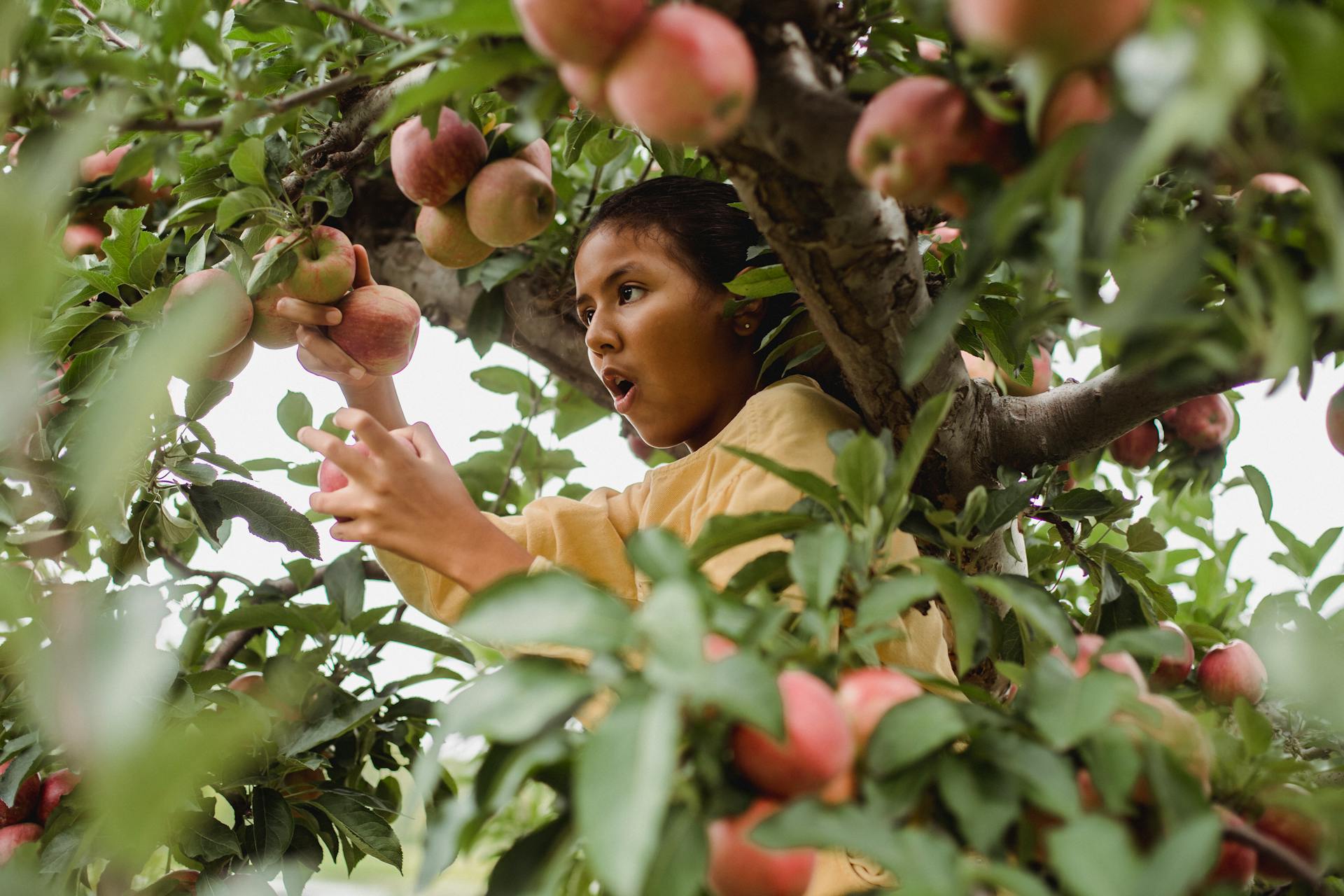
Pick & Pack Logistics Inc is a game-changer for businesses looking to optimize their supply chain. By leveraging their expertise and cutting-edge technology, you can say goodbye to inefficient logistics and hello to streamlined operations.
Their experienced team is dedicated to providing personalized solutions tailored to your unique needs. This means you can trust that your supply chain is in good hands.
With Pick & Pack Logistics Inc, you can expect significant reductions in costs and increased efficiency. Their innovative approach to logistics ensures that your products are delivered quickly and accurately to your customers.
What Is Pick & Pack Logistics?
Pick & pack logistics is a fulfillment method that involves picking and packing individual customer orders from a warehouse. This process typically takes place in a dedicated facility.
It's a vital step in the e-commerce supply chain, allowing businesses to efficiently manage and ship products to customers. Pick & pack logistics can be outsourced to a third-party logistics provider.
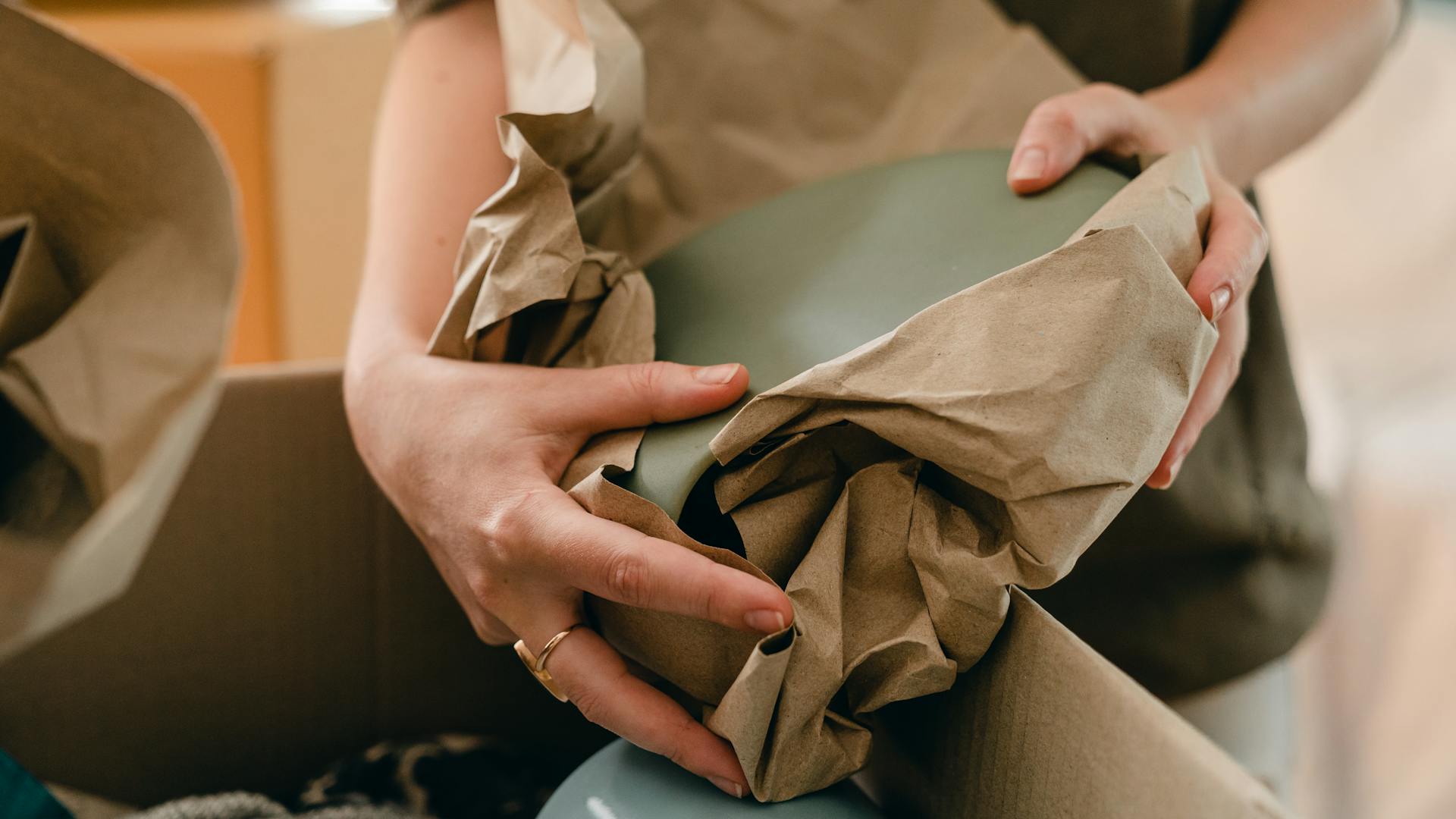
The goal of pick & pack logistics is to ensure that each order is accurately picked and packed, reducing errors and improving customer satisfaction. This involves verifying the order details and selecting the correct products.
Pick & pack logistics can be done manually or with the help of automated systems, such as pick-to-light or pick-to-voice technology.
For your interest: Order Picking
Benefits of Pick & Pack Logistics
Pick & pack logistics can be a game-changer for businesses looking to streamline their operations and improve customer satisfaction. Efficiency and accuracy are key benefits of using a pick-and-pack warehouse, as it speeds up and improves the accuracy of order fulfillment, cutting down on mistakes and wait times.
By outsourcing to a third-party logistics (3PL) provider, businesses can cut costs and work more efficiently, making the picking process more efficient. This is especially important for businesses that are growing rapidly and need to scale their operations quickly.
One of the main advantages of partnering with a 3PL provider for pick-up and pack services is scalability and flexibility. Our pick-and-pack warehouse can handle varying order volumes, making it easy to scale up during peak times.
Discover more: 3pl Last Mile Delivery
Packing is a crucial part of the pick-and-pack process, and it's where our expertise and technology really shine. We use advanced warehouse management systems and pick and pack software to streamline the picking and packing process, ensuring accuracy and efficiency.
Here are some key benefits of using a pick-and-pack service:
- Efficiency and Accuracy: Pick-and-pack speeds up and improves the accuracy of order fulfillment, cutting down on mistakes and wait times.
- Scalability and Flexibility: Our pick-and-pack warehouse can handle varying order volumes, making it easy to scale up during peak times.
- Expertise and Technology: We use advanced warehouse management systems and pick and pack software to streamline the picking and packing process, ensuring accuracy and efficiency.
By using the latest technology, such as state-of-the-art pick and pack software, we can track orders in real time, ensuring that every order is processed efficiently and accurately. This level of attention to detail is what sets us apart from other logistics providers.
Process and Strategy
Implementing the right pick-and-pack strategies can significantly enhance your warehouse operations. Batch Picking is a method that involves picking multiple orders simultaneously to save time and reduce labor costs, making it particularly effective for high-volume e-commerce fulfillment.
Zone Picking is another strategy that divides the warehouse into zones, assigning specific areas to pickers to minimize movement and increase efficiency. Wave Picking organizes the picking process into specific time slots, allowing for better coordination and resource allocation.
To make the most of your pick-and-pack process, consider utilizing a Warehouse Management System (WMS) and pick and pack software to streamline operations and improve accuracy. This can be done by implementing technology and automation.
By training your staff on efficient picking methods and providing them with access to the right tools and equipment, you can also optimize your pick and pack operations. This includes ensuring they have access to packing stations and appropriate packing materials.
Here are some effective pick-and-pack strategies:
- Batch Picking: saves time and reduces labor costs
- Zone Picking: minimizes movement and increases efficiency
- Wave Picking: organizes the picking process for better coordination
Process
The pick-and-pack process is a crucial part of ensuring customer satisfaction. Accurate picking and packing are essential to avoid errors and ensure customer satisfaction.
The pick-and-pack delivery process involves several steps, including importing orders, picking items, and packing them correctly. This process requires attention to detail and a focus on accuracy.
Using the latest technology, such as a warehouse management system (WMS) and pick and pack software, can help streamline operations and improve accuracy. This can be especially helpful in busy warehouses where efficiency is key.
Different picking methods, like piece, batch, zone, and wave picking, can also be used to improve efficiency and accuracy in operations. By choosing the right method for the job, you can reduce errors and improve customer satisfaction.
Here are some common picking methods:
By training your staff on efficient picking methods and providing them with the right tools and equipment, you can improve the overall efficiency of your pick-and-pack operations.
Strategies for Efficiency
Implementing efficient pick-and-pack strategies can significantly enhance your warehouse operations.
Batch Picking is a method that involves picking multiple orders simultaneously to save time and reduce labor costs. It's particularly effective for high-volume e-commerce fulfillment.
Zone Picking divides the warehouse into zones, assigning pickers to specific areas to minimize movement and increase efficiency.
Wave Picking organizes the picking process into specific time slots, allowing for better coordination and resource allocation.
Inefficient fulfillment processes can lead to errors, delays, and increased costs, impacting both customer satisfaction and operational profitability.
Take a look at this: Pick and Pack Fulfillment Services
Here are some effective methods to consider:
Technology and automation can also play a crucial role in streamlining operations and improving accuracy.
What Is Strategy?
A strategy is a plan that outlines how to achieve a specific goal or objective. It's a roadmap that guides decision-making and action.
A good strategy is flexible and adaptable, taking into account changing circumstances and unexpected events. This is evident in the example of Amazon, which has shifted its focus from being an online bookstore to a global e-commerce leader.
A strategy should be focused, prioritizing the most important goals and objectives. For instance, in the article, we discussed how Walmart focuses on providing low prices to its customers, which is a key component of its overall strategy.
A strategy should also be measurable, with clear metrics and benchmarks to track progress. This is essential for evaluating the effectiveness of the strategy and making adjustments as needed.
Services and Solutions
Pick & Pack Logistics Inc offers a range of services to help businesses manage their products and fulfill customer orders efficiently. Their expertise in pick and pack service ensures products are stored, picked, packed, and shipped to customers accurately and on time.
They provide 3PL services, apparel warehousing and fulfillment, automotive warehousing and fulfillment, container destuffing, contest execution and management services, crossdocking warehousing, and much more. Some of their key services include kitting and assembly, pick and pack fulfillment, POP & POS distribution, reverse logistics, and Shopify fulfillment with Shopify app integration.
Pick and pack companies like Pick & Pack Logistics Inc take care of the steps involved in order fulfillment, including picking, packing, and shipping. They offer customized packaging solutions to ensure products arrive safely and securely. With their expertise, businesses can enjoy rapid fulfillment, flexibility, and tailored packaging options.
Here are some of the key services offered by Pick & Pack Logistics Inc:
- Rapid Fulfillment
- Flexibility
- Tailored Packaging
- Automated Efficiency
- Global and Local Distribution
Their customized packaging solutions include standard boxes, custom-made packages, and more, helping protect shipments during transit and ensuring products arrive in perfect condition. Pick & Pack Logistics Inc also provides logistics support, order management, and warehousing services to help businesses ensure their products reach customers on time and in perfect condition.
Technology and Efficiency
Technology and efficiency are crucial components of a successful pick & pack logistics operation. By leveraging advanced technology, companies can streamline processes, reduce errors, and cut costs.
Our state-of-the-art pick and pack software allows us to track orders in real time, ensuring accuracy and efficiency in operations. This is made possible by our advanced warehouse management systems (WMS), which automate and optimize overall operations, keeping a live record of all inventory and orders.
We utilize various picking methods, including piece, batch, zone, and wave, to ensure efficiency and accuracy in operations. This, combined with our superior shipping software, allows us to obtain the optimal mix of cost and speed of delivery.
Here are some of the key technologies we use to drive efficiency and accuracy:
- Advanced Warehouse Management Systems (WMS)
- Real-time order tracking
- Pick and pack software
- Superior shipping software
These technologies enable us to provide top-level, white-glove service to our clients with minimal delays or disruptions, even during peak times.
What Is Warehouse Management?
Warehouse management is a critical component of efficient order fulfillment. It's the backbone of a well-oiled logistics machine.
A warehouse management system (WMS) is the key to automating and optimizing overall operations. This system keeps a live record of all inventory and orders, giving businesses real-time visibility to instantly find any order status and see what's happening with their merchandise.
This level of visibility is crucial for maintaining accuracy, with employees updating each order at every step. It's the WMS that allows businesses to focus on efficiency, accuracy, and scalability.
Our WMS is designed to handle fluctuating order volumes, making it easy to scale up during peak times. This flexibility is especially important for online ordering, which can vary greatly depending on the day or time of year.
Here are some benefits of a robust WMS:
- Automates and optimizes overall operations
- Keeps a live record of all inventory and orders
- Provides real-time visibility to instantaneously find any order status
- Helps maintain accuracy and scalability
Technological Integration:
Technological integration is crucial for efficient pick-and-pack operations. It's essential to have an advanced Warehouse Management System (WMS) that can automate and optimize overall operations, maintaining a live record of all inventory and orders for instant order status checking.
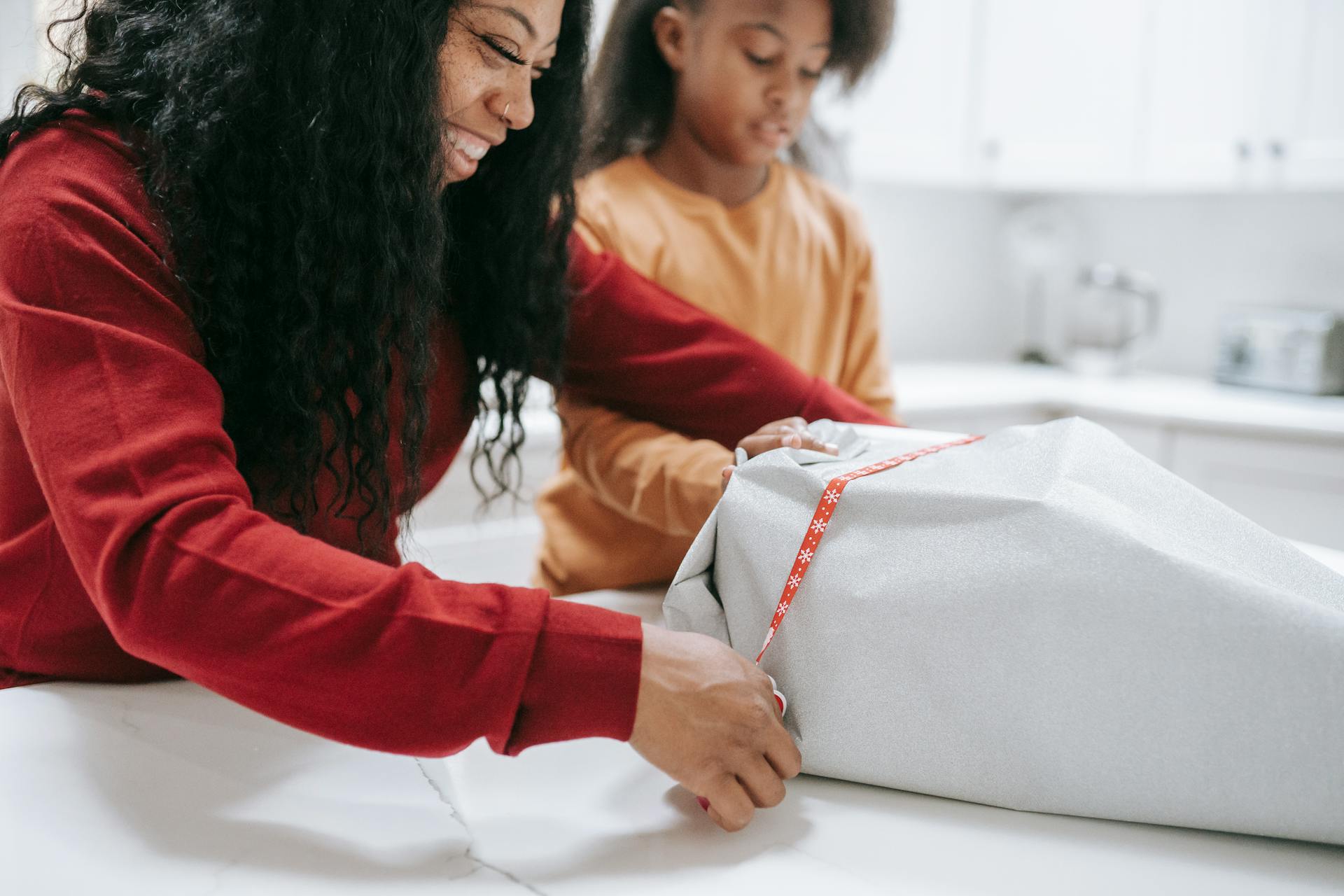
A WMS can help drive accuracy, with employees updating each order at every step. This system is also the key to maintaining accuracy and scalability, allowing businesses to provide top-level service to their clients with minimal delays or disruptions.
To ensure efficient operations, a 3PL provider should use the latest technology, paired with different picking methods (piece, batch, zone, wave) for efficiency and accuracy. This can include using advanced pick and pack software to track orders in real time.
Some key features of an effective WMS include:
- A live record of all inventory and orders
- Automated and optimized operations
- Real-time order status checking
- Scalability and flexibility to handle varying order volumes
By leveraging these technological advancements, businesses can streamline their pick-and-pack operations, reduce errors, and improve overall efficiency.
Choosing a 3PL Partner
Choosing a 3PL Partner can be a daunting task, but it's essential to research and find out what other customers are saying about the company before deciding.
Many businesses face the same challenges when choosing a pick and pack service provider, so it's crucial to consider what other customers have experienced. SHIPHYPE, for instance, provides a comprehensive range of services and can help businesses get started quickly.
Researching customer reviews can give you valuable insights into a 3PL partner's strengths and weaknesses. Our team can answer any questions and provide additional information about their pick and pack services, so don't hesitate to reach out.
Recommended read: 3pl Pick and Pack
Key Characteristics for Choosing a 3PL Partner
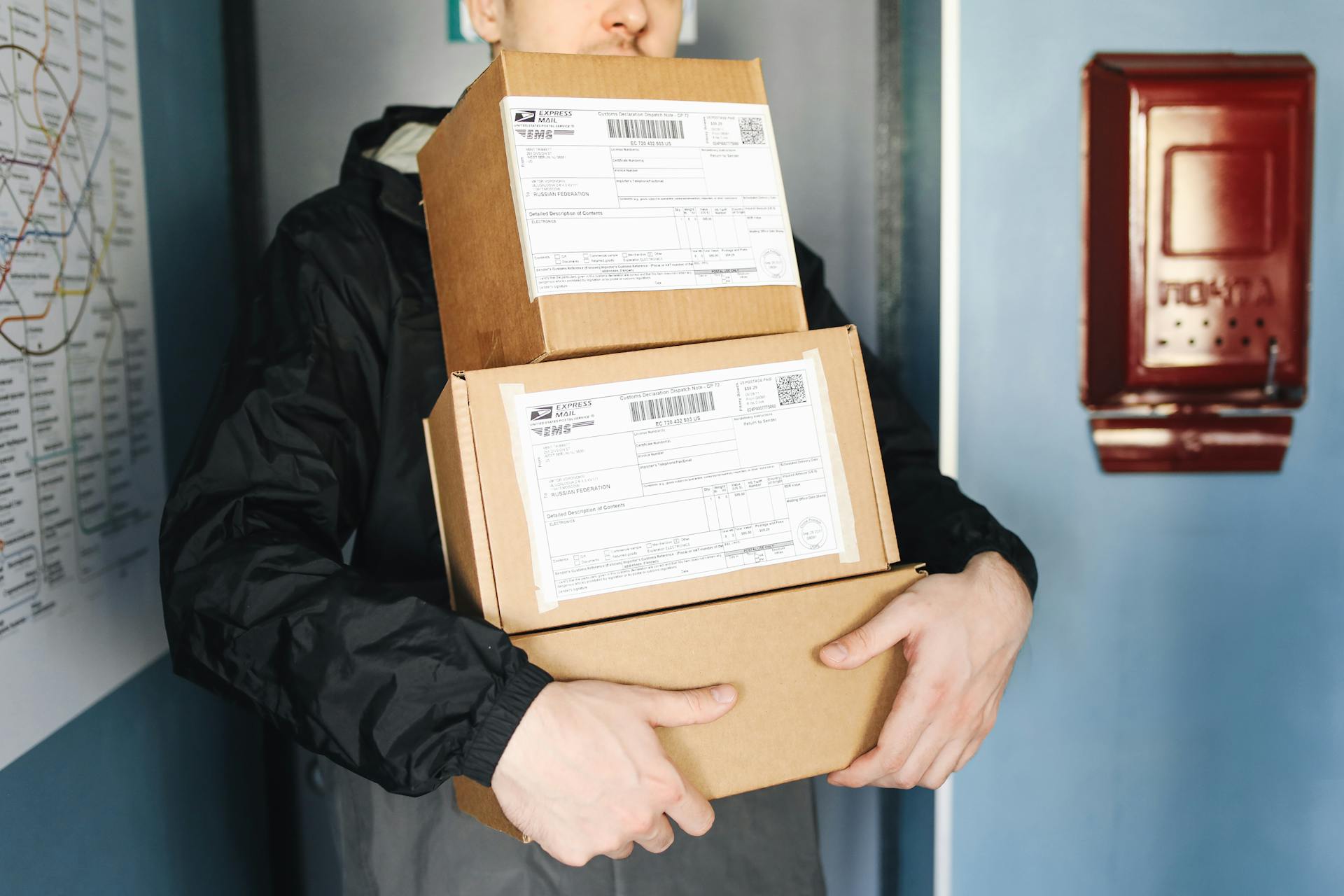
Choosing a 3PL partner can be a daunting task, but it doesn't have to be. By considering the right characteristics, you can find a partner that meets your needs and helps you achieve your business goals.
Scalability and flexibility are essential for any business, and a good 3PL partner should be able to handle varying order volumes. This means they can scale up during peak times and adjust to changes in demand.
Expertise and technology are also crucial for a 3PL partner. They should use advanced warehouse management systems and pick and pack software to streamline the picking and packing process, ensuring accuracy and efficiency.
A good 3PL partner should be able to handle your business's unique needs, and having local expertise and knowledge is a big plus. This means they understand the local market and can provide personalized services tailored to your business.
Here are some key characteristics to look for in a 3PL partner:
- Scalability and flexibility to handle varying order volumes
- Expertise in using advanced warehouse management systems and pick and pack software
- Local expertise and knowledge of the market
- Commitment to customer satisfaction and accuracy
Differences Between Service Provider and Center Provider
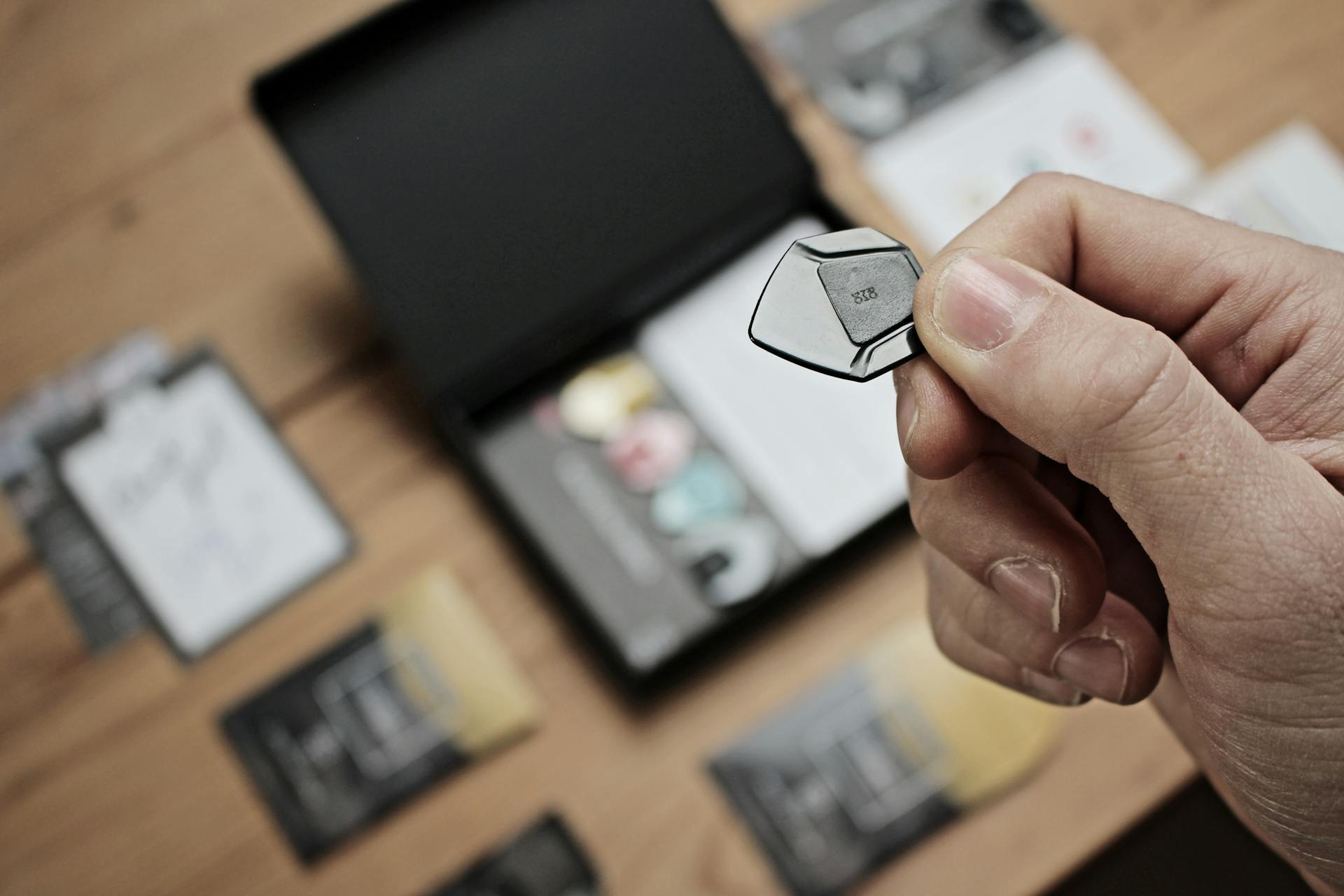
If you have a smaller business with many individual orders, a picking service provider might be the way to go. They're good at handling small quantities and ensuring each pick and pack order fulfillment is correct.
A fulfillment center, on the other hand, can store large quantities of your products, which is a big plus if you have a lot of inventory. They can also manage your inventory for you, which is a huge time-saver.
If you have a bigger pick and pack operation with more complex needs, a fulfillment center could be a better fit. They can handle tasks like returns and even some customer service, which can be a big help for businesses with a lot of customer interactions.
In the end, it's all about finding a 3PL partner that meets your specific needs.
For more insights, see: What Is Pick and Pack Fulfillment
Why Choose Pick & Pack Logistics?
At Pick & Pack Logistics, we take customer service and product quality seriously, offering unmatched attention to detail in our pick and pack service.
Our team of experts will make sure your packages get out safely and on time, whether you need help with one order or hundreds. We understand that pick and pack service is critical to a successful operation.
Here are the competent reasons why you should choose us as your service provider: we offer reliable and efficient order fulfillment, ensuring that your customers receive their orders promptly and in good condition.
Why Choose Us in Portland?
We're your local partner dedicated to your success. Our deep understanding of the Portland market helps us provide personalized and efficient services. We know what works best for businesses here.
We go the extra mile to ensure your customers receive their orders on time and in perfect condition. Our warehouse management software ensures accuracy and efficiency, reducing errors and returns.
Here are some key benefits of choosing a local partner like us:
- Local Expertise and Knowledge: We have a deep understanding of the Portland market and can provide personalized services tailored to your business needs.
- Commitment to Customer Satisfaction: We prioritize timely and accurate order fulfillment to ensure your customers are happy and loyal.
Why Choose ShipHype
At ShipHype, they take customer service and product quality seriously, which is a huge plus for businesses that rely on pick and pack services.
Their team of experts will make sure your packages get out safely and on time, whether you need help with one order or hundreds.
Their attention to detail is unmatched, which is critical to a successful operation.
They understand that pick and pack service is crucial, and they're dedicated to delivering high-quality results.
Their team is competent and skilled, able to handle any volume of orders with ease.
Order Management and Shipping
Packed orders are dispatched via an optimized distribution network, ensuring efficient delivery times both locally and globally.
Prompt shipping is crucial for customer satisfaction, and delays can significantly harm your company’s reputation and customer retention. Efficient delivery times are essential for building trust with customers.
IDS provides a comprehensive inventory management system and tracking services that ensure all orders are fulfilled quickly and accurately. This system is also the key to maintaining accuracy, with employees updating each order at every step.
Here are some of the services offered by IDS for order management and shipping:
- Kit-Making
- Cartonization
- Sorting
- Product Labeling
- Shipping Label Printing
- Shrink-Wrap / Bundle Pack
- Collating
- Product Testing
- Custom Pallet Displays
- POP Assembly
- Final Packing
- Repacking
- D2C Delivery
Order Management
Order management is a vital part of the fulfillment process, ensuring that orders are processed quickly and accurately. IDS provides a comprehensive inventory management system to help businesses manage their orders from initial entry to packing and delivery.
Pick and pack companies can help businesses manage their orders, making it easier to keep track of inventory and fulfill orders efficiently. This can be a huge time-saver, especially for businesses with a high volume of orders.
IDS utilizes various picking methods to ensure maximum accuracy in delivery, choosing the most efficient method for both time and money. These methods include different picking strategies that can be tailored to a business's specific needs.
A good order management system can help businesses improve their customer satisfaction rates by ensuring that orders are fulfilled quickly and accurately. This can lead to increased customer loyalty and repeat business.
IDS's process-driven approach enables businesses to focus on their marketing and sales efforts while knowing that their order fulfillment is taken care of. This can be a huge weight off a business owner's mind, allowing them to focus on growth and expansion.
Explore further: Best Last Mile Delivery Companies
Shipping
Shipping is a critical part of the order management process, and it's essential to get it right to ensure timely and cost-effective delivery.
Packed orders are dispatched via an optimized distribution network, ensuring efficient delivery times both locally and globally.
IDS Technology takes shipping to the next level with its ProParcel shipping solution, which cuts through the differences between carriers to accurately pinpoint and automatically select the most cost-efficient shipping carrier and shipping method for each order.
This system is customizable to your preferences, allowing you to meet your company's customer expectations.
IDS also offers flexibility in shipping, including the ability to add additional stations as needed, allowing for top-level, white-glove service to clients with minimal delays or disruptions.
The company's West Coast Fulfillment Center provides a dedicated shipping solution, with a range of services including kit-making, cartonization, and shipping label printing.
Here are some of the shipping services offered by IDS Technology:
- Kit-Making
- Cartonization
- Sorting
- Product Labeling
- Shipping Label Printing
- Shrink-Wrap / Bundle Pack
- Collating
- Product Testing
- Custom Pallet Displays
- POP Assembly
- Final Packing
- Repacking
- D2C Delivery
Shipping Delays
Shipping delays can significantly harm your company's reputation and customer retention. Prompt shipping is crucial for customer satisfaction.
Related reading: Dangerous Goods Shipping and Handling Services in Dubai
Order management systems can help prevent shipping delays by ensuring all orders are fulfilled quickly and accurately. Companies that use pick and pack services can manage their orders from entry to delivery.
Technology plays a key role in preventing shipping delays. A warehouse management system (WMS) can automate and optimize operations, keeping a live record of all inventory and orders.
This real-time visibility allows clients to instantly find any order status and see what's happening with their merchandise. It's the WMS that maintains accuracy, with employees updating each order at every step.
Shipping delays can be avoided by using a system that's customizable to your preferences. The ProParcel shipping solution cuts through the differences between carriers to automatically select the most cost-efficient shipping carrier and shipping method for each order.
A flexible approach to shipping is also essential. IDS offers flexibility across the board, including flex labor, integrated robotic systems, and the ability to add additional stations as needed. This allows for top-level, white-glove service with minimal delays or disruptions.
Additional reading: Door to Door Container Shipping
Inventory Management and Efficiency
At Pick & Pack Logistics Inc, we understand the importance of efficient inventory management. Efficient inventory management is fundamental for avoiding overstock or stockout situations.
We leverage advanced technology to streamline processes, reduce errors, and cut costs. This approach ensures that our services are a cost-effective choice for your fulfillment needs.
A comprehensive inventory management system is crucial for tracking and managing orders. This system ensures all orders are fulfilled quickly and accurately.
We utilize advanced warehouse management systems to optimize inventory levels and ensure timely order fulfillment. Various picking methods, such as piece, batch, zone, and wave picking, are used to ensure efficiency and accuracy in operations.
By using superior shipping software, we can obtain the optimal mix of cost and speed of delivery. This approach enables us to provide fast and reliable shipping options to our clients.
Retail Ready & Shelf Ready
At Pick & Pack Logistics Inc, we understand the importance of getting your products to market quickly and efficiently. Retail-ready packaging (RRP) and shelf-ready packaging (SRP) are crucial components of a successful fulfillment strategy.
Check this out: Blister Pack Packaging
Having a fully-optimized RRP or SRP operation ensures that your products arrive at their final destination in perfect condition. This is especially important for industries where products are frequently shipped and received.
Branded boxing is a key aspect of RRP, allowing you to customize the packaging to match your brand's image. Custom packaging is also available to match your specific product needs.
Eco-friendly packaging options are also available, allowing you to reduce your environmental impact while still providing a professional presentation. Branded mailers and inserts can be used to add a personal touch to your shipments.
Here are some of the key features of our RRP and SRP services:
- Branded boxing
- Custom packaging
- Eco-friendly packaging
- Branded mailers & inserts
Frequently Asked Questions
What is the pick pack ship process?
The pick-pack-ship process is a streamlined order fulfillment method that involves picking products, packing them correctly, and shipping them out efficiently. It's a standard process used by most companies to get products to customers quickly and reliably.
Sources
- https://www.afewimports.com/warehouse-fulfillment/streamline-your-fulfillment-with-a-few-imports-logistics-pick-and-pack-warehouse
- https://www.ppfd.com/pick-and-pack-fulfillment/
- https://shiphype.com/pick-and-pack-service/
- https://idsfulfillment.com/pick-and-pack
- https://www.wsinc.com/service/fulfillment/custom-packaging-repacking-assembly/
Featured Images: pexels.com