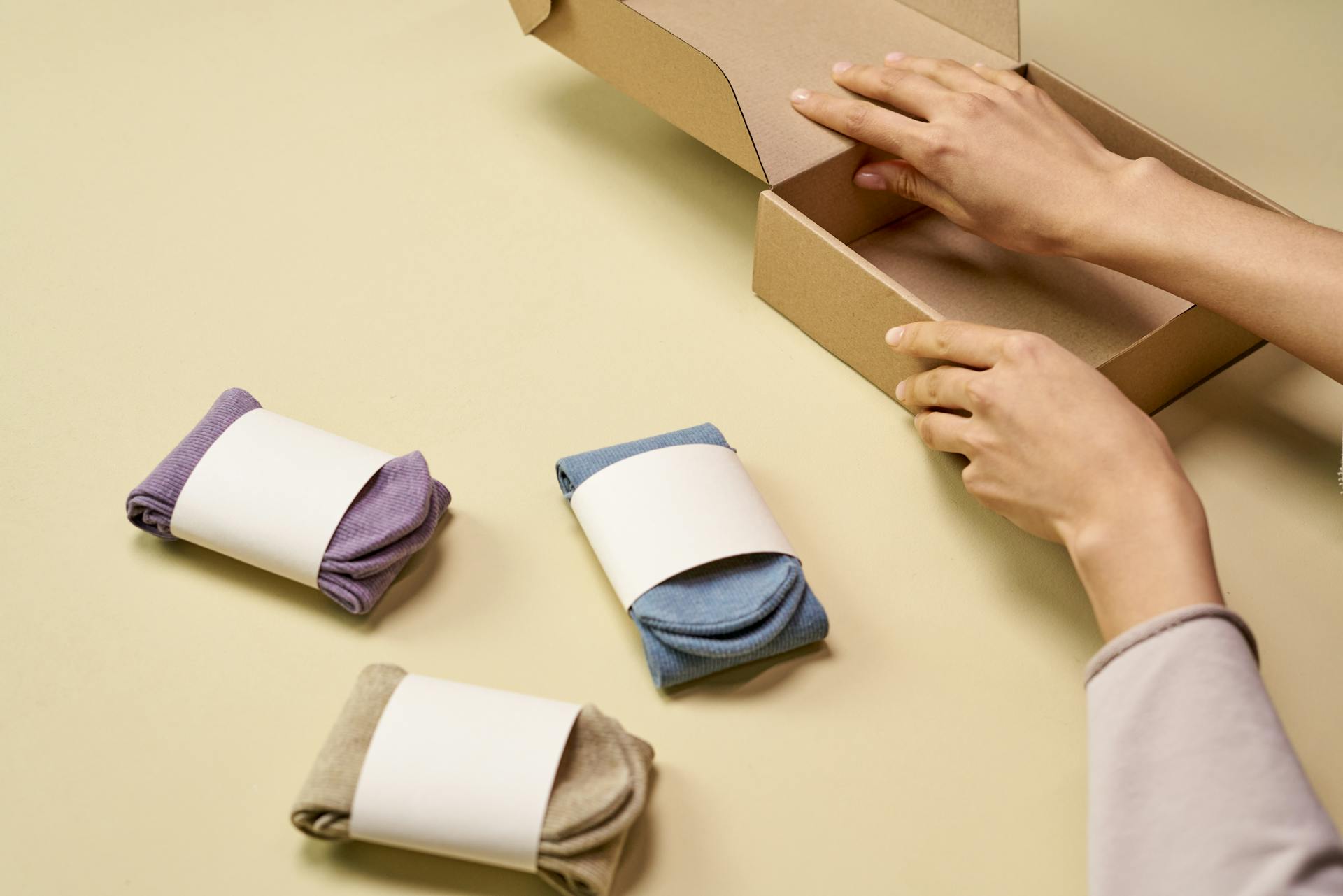
There are several types of paper corrugated machines, each with its own unique features and capabilities.
The most common type is the single-facer machine, which produces a single layer of corrugated board.
It's often used for producing small quantities of corrugated board, such as in craft or hobby applications.
The double-facer machine, on the other hand, produces two layers of corrugated board, making it more suitable for larger production runs.
This type of machine is often used in industrial settings where high volumes of corrugated board are needed.
The triple-facer machine is a more complex and expensive option, but it produces three layers of corrugated board, offering even greater strength and durability.
It's often used in applications where the corrugated board needs to withstand heavy loads or harsh environments.
Machine Types
There are various types of paper corrugated machines available, each with its own unique features and capabilities. The Oblique Type Single Face Paper Corrugating Machine is suitable for converting paper into corrugated 2ply rolls, with a capacity of 0-10 ton/day.
The High Speed Single Face Corrugation Machine has a capacity of 1-3 Ton/day and is an automatic machine, making it ideal for high-volume production.
Some common features among these machines include a frequency of 50/60 Hz and a voltage of 220 V. The Size of the Oblique Type machine is 45", while the High Speed machine has a Max Working Width of 1600 mm.
Oblique
Oblique machines are used in various industries, including paper production. They are designed to handle specific tasks with high efficiency.
The Oblique Type Paper Corrugation Machine has a capacity of 1 to 2 Ton/day. This makes it suitable for small to medium-sized operations.
The machine is semi-automatic, which means it requires some human intervention during the production process. However, it can still increase productivity and reduce labor costs.
The Oblique Type Single Facer Corrugation Machine has a capacity of 5 tonnes per day, making it a more heavy-duty option. This machine is fully automatic, which means it can run with minimal human intervention.
Intriguing read: Automatic Strapping Machine
The machine has a speed of 40 meters/min, which is relatively fast compared to other types of corrugation machines. This makes it ideal for high-volume production.
Here are some key specifications of the Oblique Type Single Facer Corrugation Machine:
The Oblique Type Single Facer Corrugation Machine is also ISO certified, which ensures that it meets international quality and safety standards. This is an important consideration for businesses that need to export their products or work with international clients.
Nagpal High Speed
Nagpal High Speed machines are designed to provide efficient and reliable performance. They are capable of producing 10 tonnes per day.
The Nagpal High Speed Fingerless Corrugation Machine has a speed of 150 meters per minute. This makes it a great option for industries that require high production rates.
The machine is equipped with a hydraulic reel stand with 5 horsepower. This provides the necessary power to drive the machine's components.
The Nagpal High Speed Fingerless Corrugation Machine is made from high-quality 48 CrMo alloy steel. This material is known for its strength and durability.
Here are some key features of the Nagpal High Speed Fingerless Corrugation Machine:
The machine's production capacity is 10 pieces, and it can be delivered within a month. The packaging details are loose, and the payment terms include L/C (Letter of Credit) and T/T (Bank Transfer).
Features and Options
The paper corrugated machine is a versatile piece of equipment that offers a range of features and options to suit various needs.
One of the key features is the ability to produce different types of corrugated boards, including single-faced, double-faced, and triple-faced boards.
The machine's speed and efficiency are also noteworthy, with some models capable of producing up to 100 meters per minute.
With the ability to customize the machine to specific production requirements, users can optimize their output and quality.
The machine's precision cutting feature ensures accurate cuts and minimal waste.
Automatic
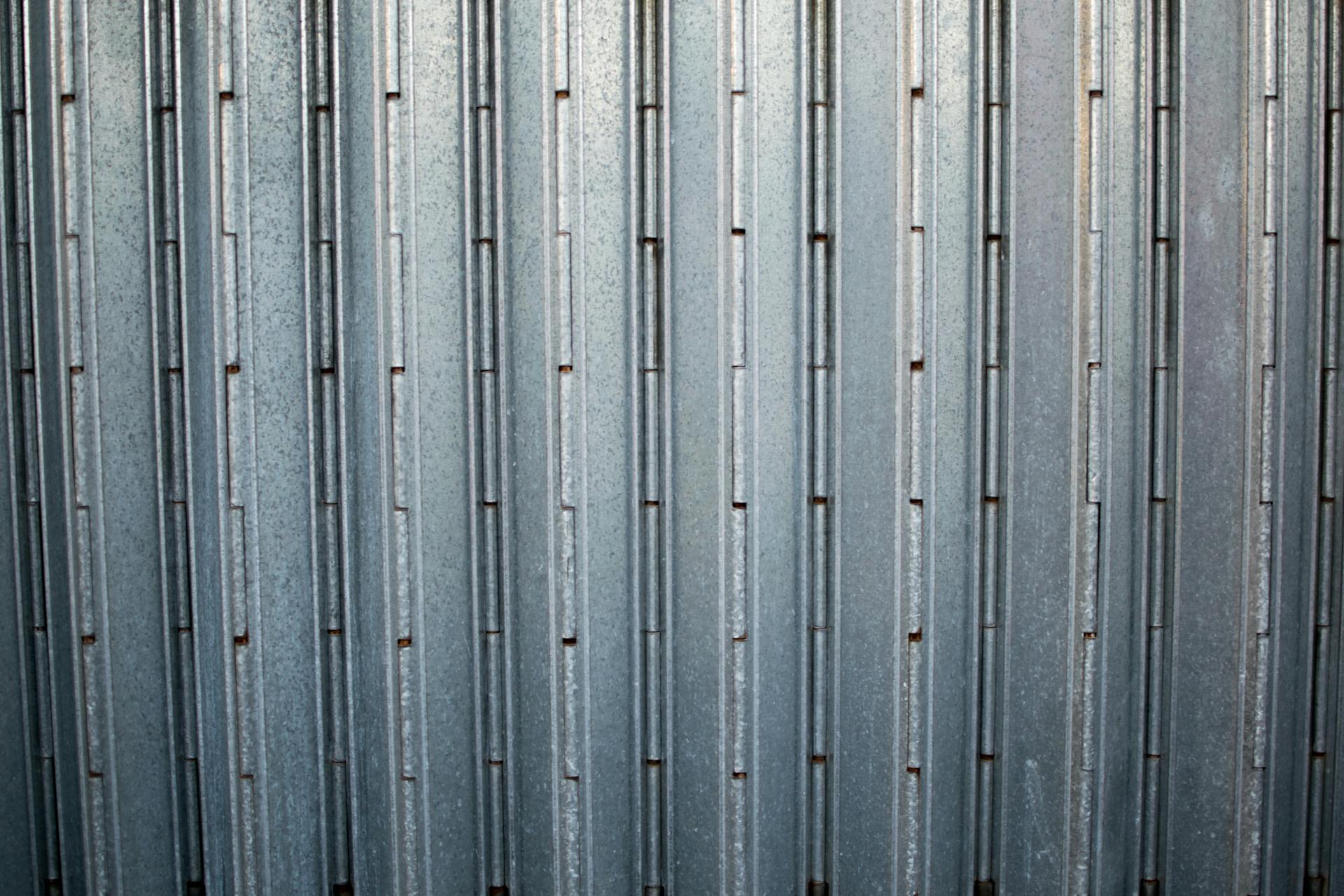
When investing in automatic machinery, it's essential to consider the level of automation you need. Our paper preheaters, for instance, come with an automatic wrap angle feature.
The automatic rotary and wrap angle on our paper preheaters can be adjusted to suit different paper widths. This feature is available on machines with widths ranging from 1200 to 3300mm.
Our automatic machinery is designed to minimize manual labor and increase efficiency. The automatic 5 ply corrugated board production line, for example, is a fully automated system that can produce high-quality corrugated boxes.
Here are some examples of our automatic machinery:
- Automatic Rotary and Wrap Angle (available on paper preheaters)
- 5 Ply Fully Automatic Corrugated Box Making Machine
- Down Stacker For Automatic Corrugated Board Plant
Our machines are not just automated, but also come with dedicated after-sales service. This includes an overseas service center and engineers available to service machinery overseas.
Features and Options
This machine is designed with features that enhance its performance and efficiency. The Corrugated Package Machine can be equipped with a Peripheral Preheater that operates in half or full cycle mode.
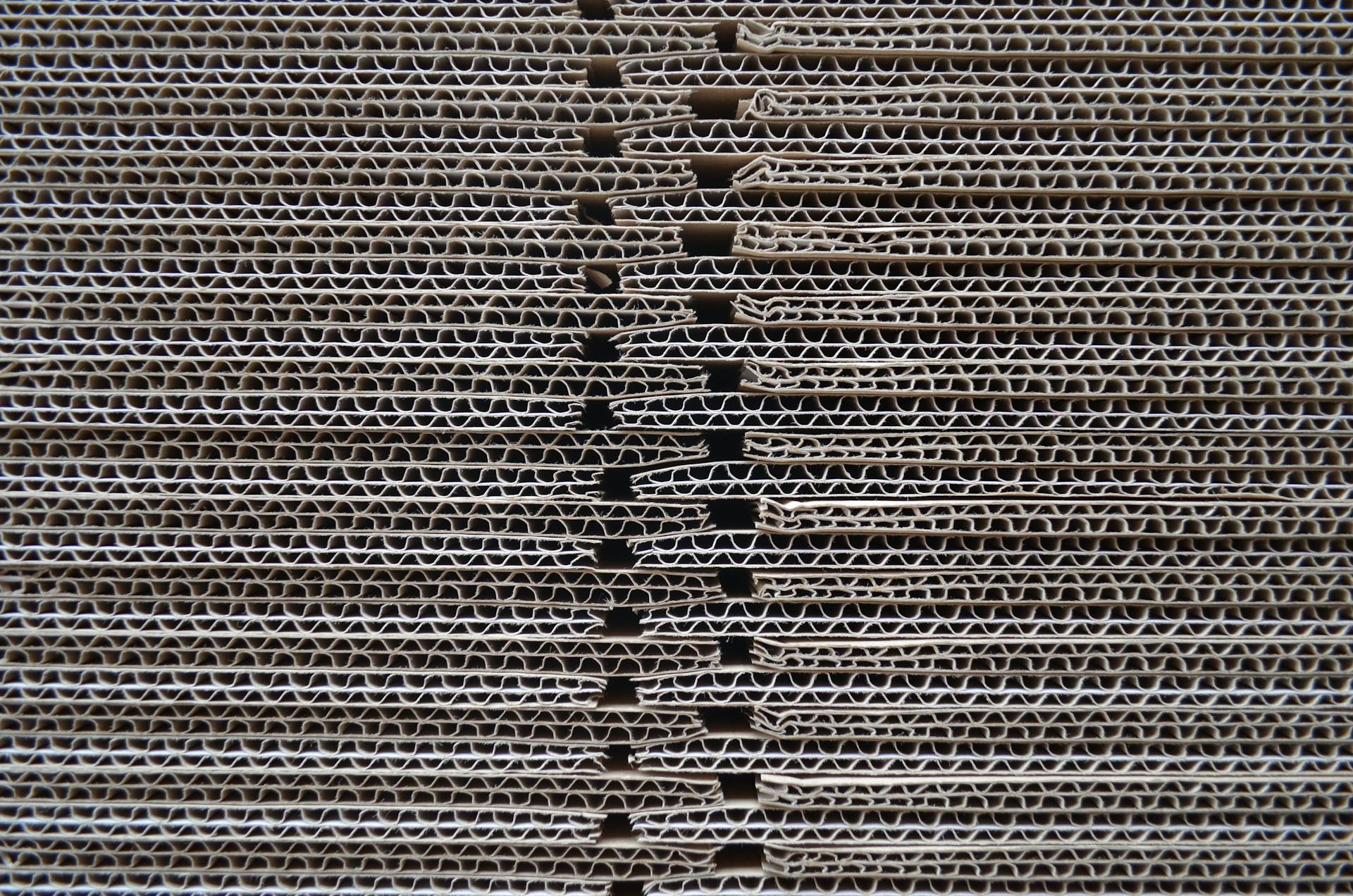
Temperature control is automatic, thanks to built-in temperature sensors. These sensors ensure that the machine operates within a precise temperature range.
The machine's speed can be adjusted to suit different production needs, ranging from 100 to 350 meters per minute. This flexibility allows users to optimize their production workflow.
Auto control with sensors and valves is a key feature of this machine. This advanced control system ensures that the machine operates smoothly and efficiently.
Components and Parts
If you're looking for spare parts for your paper corrugated machine, there are several key components to consider. The Plastic Creasing Matrix is a crucial part of the machine, helping to shape the corrugated sheet into the desired form.
You may also need to replace the Handle Hole Attachment, which helps secure the handle in place. The Pushers for Corrugated Sheet are another essential part, ensuring that the sheet is properly pushed through the machine.
Consider reading: Corrugated Plastic Sheets for Signs
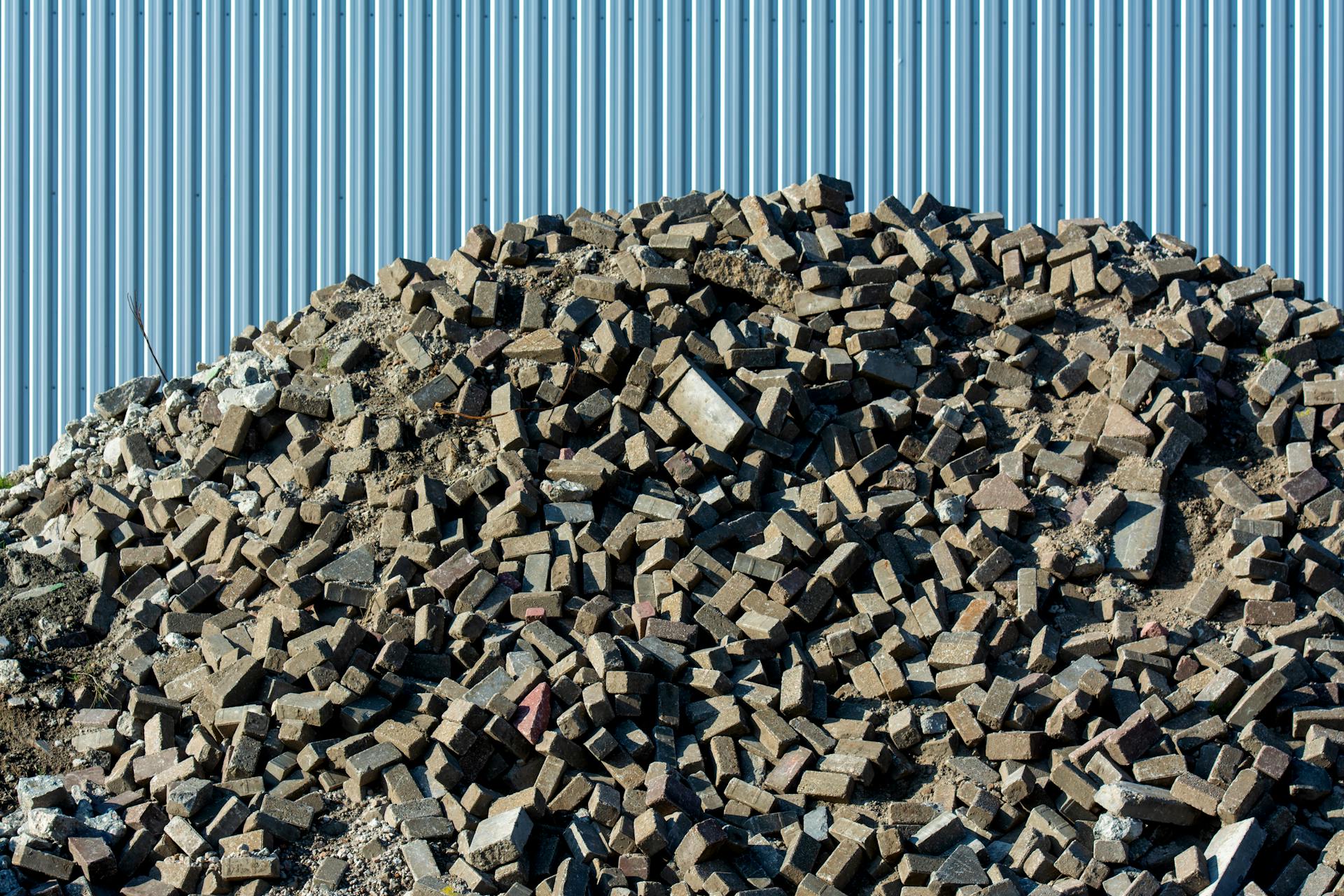
Here are some specific spare parts you may need to replace:
- Plastic Creasing Matrix
- Handle Hole Attachment
- Pushers for Corrugated Sheet
In addition to these parts, you may also need to replace the Flexo Printer Slotter CAM Clutch Bearing, which helps maintain the smooth operation of the machine. The Anvil Cover (HB9405) is another important part, protecting the machine from damage and wear.
Vertical
Vertical components play a crucial role in various machinery, including paper corrugation machines.
The diameter of the rolls in these machines can vary, with some having a diameter of 200 mm, as seen in Examples 1 and 2.
The material used for the rolls is often EN-9 (Forged), which provides the necessary strength and durability for industrial use, as mentioned in Examples 1 and 2.
The motor power required for these machines can range from 7 HP, as seen in Examples 1 and 2, to other specifications.
The motor brand can also vary, with some machines using Crompton motors, as shown in Example 2.
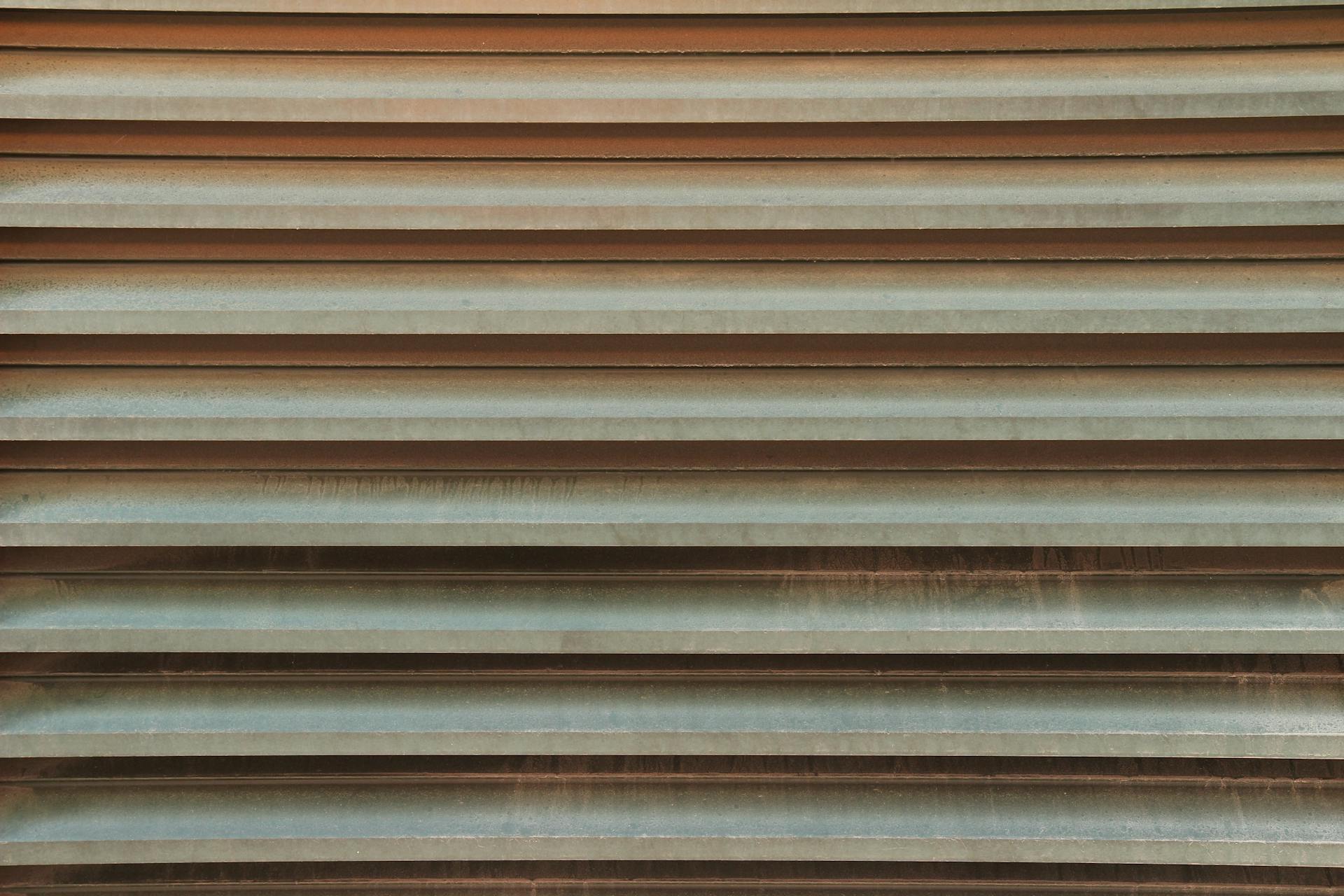
The machine type is often vertical, as seen in Examples 3 and 4, which allows for efficient and space-saving production.
The output paper width can also vary, with some machines capable of producing paper widths from 0-500 mm to 2000 mm or more, as mentioned in Example 3.
The speed of these machines can also be adjusted, with some capable of reaching speeds of up to 50 meters per minute, as seen in Example 3.
Here is a list of some of the key features of vertical components in paper corrugation machines:
The working height of these machines can also vary, with some having a working height of 1050 mm, as seen in Example 3.
The production capacity of these machines can also vary, with some capable of producing up to 10 sets per month, as mentioned in Example 3.
Penumatic
The Penumatic Single Facer Paper Corrugation Machine is a significant component in the paper corrugation process. It's used in industrial settings.
One crucial aspect of this machine is its power consumption, which is approximately 50 kW. This is a key consideration for businesses looking to minimize their energy costs.
The machine's working air pressure is another important factor, ranging from 0.6 to 0.9 Mpa. This pressure is essential for the machine's operation and can impact the overall quality of the corrugated paper.
The Penumatic Single Facer Paper Corrugation Machine can operate at two different speeds: design speed and economy speed. The design speed is 80 m/min, while the economy speed is 60 m/min.
Here are the key specifications of the Penumatic Single Facer Paper Corrugation Machine:
Peripheral Preheater
The Peripheral Preheater is a crucial component in many manufacturing processes, including corrugated package machines. It's used to preheat materials before they're processed.
This preheating process can be done in either a half or full cycle, depending on the specific needs of the machine. Auto temperature control is also a standard feature, which ensures that the temperature is precisely managed.
The Peripheral Preheater can operate at a speed of 100-350m/min, making it a highly efficient component.
Sheet Cutting
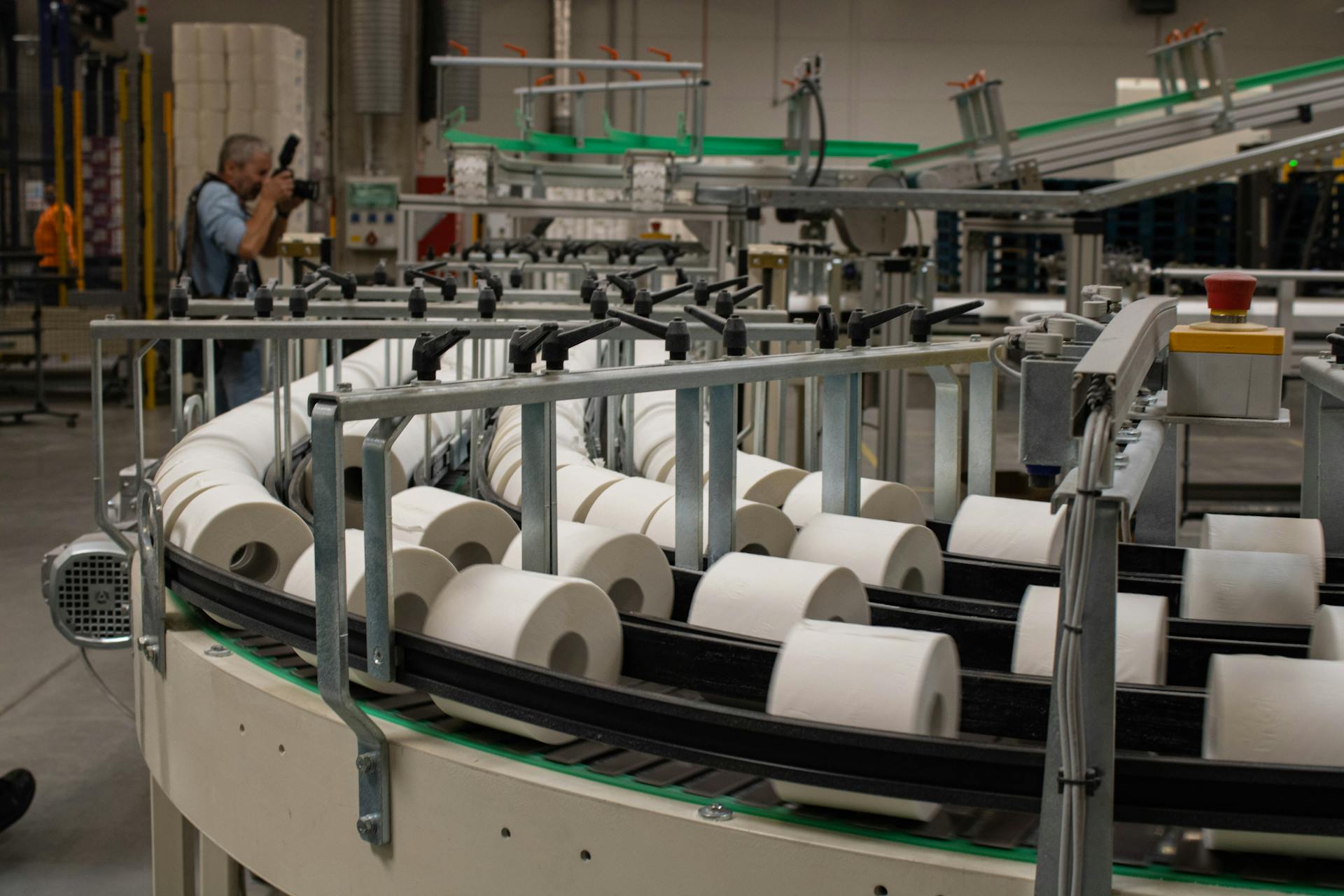
Sheet cutting is a crucial process in various industries, including paper and corrugated board manufacturing. The machines used for this purpose come in different types, such as manual and semi-automatic.
A manual corrugated paper board cutting machine, like the MMT00181 model, has a capacity of 1-3 Ton/day and can cut paper, corrugated liners & boards. It's fitted with front and back guides for measurement and a perfectly balanced blade for smooth cutting.
Semi-automatic machines, like the SN003 model, are designed for high production and instant cutting of sheets or ply corrugated board without damaging flutes & liner paper. They can be used as an independent unit or synchronized with a corrugation system.
The cutting precision of these machines is impressive, with some models offering a cutting precision of 1 mm. The effective width and cutting length of these machines can also be adjusted to suit different needs.
Here are some key features of sheet cutting machines:
Some machines, like the Reel to Sheet Cutting Machine, have a special characteristic of oil tub equipment with oil lubricating pump and a PIV tools container for adjusting the sheet to the specified length. They also have a robust design and are easy to operate.
Nagpal N.C Thin Blade Scorer
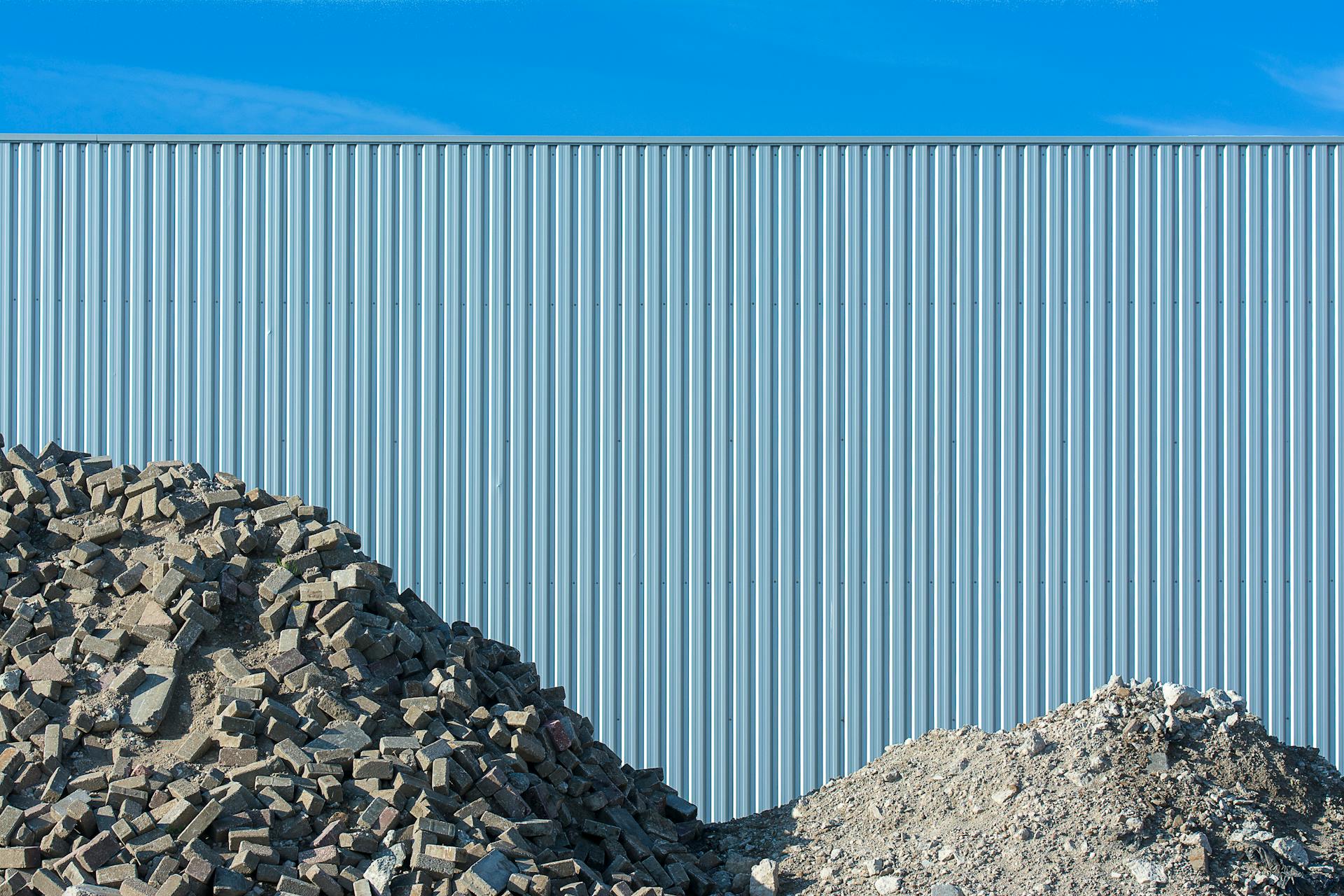
The Nagpal N.C Thin Blade Scorer is a high-speed cutting machine designed for corrugated board slitting and scoring. It features a production capacity of 200 meters per minute.
The machine is equipped with a fine cutting edge enabled by its thin blade, allowing for precise cuts at high speeds. Automatic grinding and lubrication systems keep the blade sharp at all times.
The Nagpal N.C Thin Blade Scorer has a width of 1800mm and is an automatic machine type. It's powered by an electric motor with a voltage of 380V.
Here are the motor specifications for the machine:
This machine is designed for high-speed order changes, with a computerized system that can store up to 999 orders and prioritize them for efficient processing.
Combined Rotary Creaser Slotter
The Combined Rotary Creaser Slotter is a versatile machine that can handle various tasks with ease. It's an electric driven type, making it efficient and reliable.
This machine is designed to work with semi-automatic automation, allowing for a balance between human intervention and automated processes. It's perfect for industries that require high production volumes.
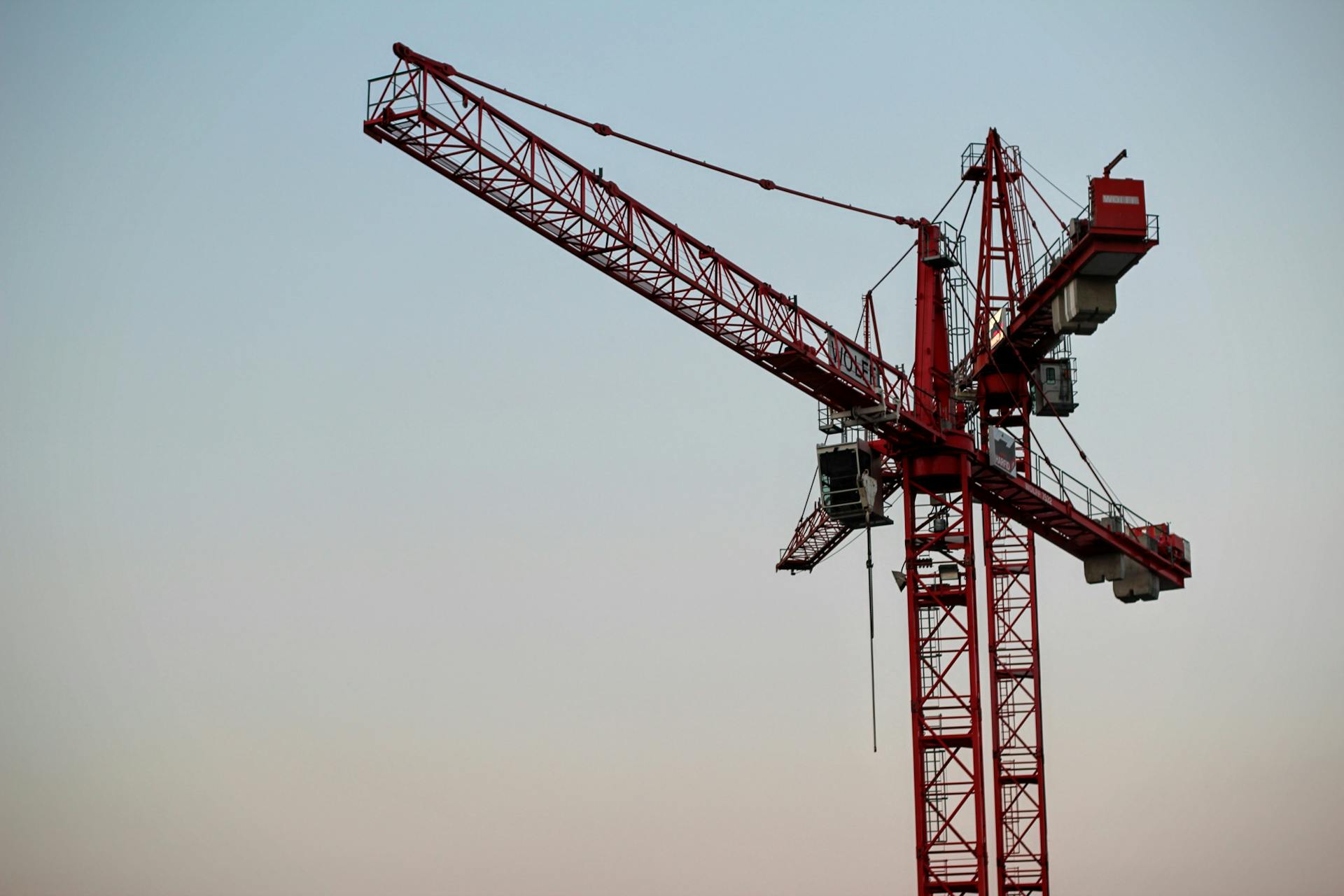
The Combined Rotary Creaser Slotter can process up to 70 sheets per minute, making it a great option for businesses that need to meet tight deadlines. Its speed regulation feature ensures that the machine can adapt to different production requirements.
The machine is made of high-quality materials, including carbon steel and cast iron, which provide durability and resistance to wear and tear. The gears are lubricated by a spray type cycle lubrication system, reducing the risk of mechanical failures.
Here are some key specifications of the Combined Rotary Creaser Slotter:
The machine's main motor and glue head are imported from Taiwan, ensuring that they meet high international standards. Overall, the Combined Rotary Creaser Slotter is a reliable and efficient machine that can help businesses streamline their production processes.
Lead Edge Feeder Printer Slotter Die Cutter Stacker
The Lead Edge Feeder Printer Slotter Die Cutter Stacker is a highly efficient machine that can produce 110pcs/Min, which is the economic speed. This speed can vary based on the board size and quality.
It's powered by a 380v AC voltage, which is a standard requirement for such machines.
The machine is designed to print on corrugated carton board, making it perfect for packaging industries.
It's a flexo type printing machine that can produce multi-color output.
The machine is available in the PS-Y3 model, which is a specific type of machine made by Nagpal Natraja.
Here are the performance features of the feeding unit:
The printing unit has several performance features, including registration adjusted by feeder PLC or section’s PLC. Boards pull wheels fast lock lateral move system is also available.
Manual gap pressure adjust and automatic lock device are also part of the printing unit's features.
The slotter unit uses a six-axis design, which allows for slotting size computerized adjusting and servo motor control. This design also enables middle knife movable and variable boxes available.
2 Ply Slitter and Stacker
The 2 Ply Slitter and Stacker is a crucial component in corrugated board production. It's capable of handling a significant capacity of 10-20 ton/day.
This machine is designed to work automatically, making it a great addition to any production line. Automation grade is indeed automatic.
The output paper width can range from 1500-2000 mm, which is quite impressive. This means it can handle a variety of paper sizes and types.
One notable feature of the 2 Ply Slitter and Stacker is its computerized cutt off and automatic stacker. This makes the process much faster and more efficient, with speeds up to 130 mtrs per min.
Here's a brief overview of the machine's specifications:
The 2 Ply Slitter and Stacker is indeed a fully automatic machine, with auto ejecting capabilities. This makes it a great choice for high-volume production lines.
Semi-Automatic Folder Gluer
The Semi-Automatic Folder Gluer is an impressive machine that can handle a wide range of tasks. It has a size of 85 inches.
This machine is capable of processing 50 pieces per minute, which is quite fast. It's perfect for high-volume production.
The automation grade of this machine is semi-automatic, which means it requires some human intervention but also has automated features. The model name is RNN SEMI-AUTOMATIC FOLDER GLUER.
The maximum size of the machine is 2800mm, which is significantly larger than its predecessor's maximum size of 2460mm. This indicates that the newer model can handle larger items.
The machine can process items with a maximum size of (L + W) X 2mm, which is 2800mm. The minimum size it can process is (L + W) X 2mm, which is 340mm.
Here's a summary of the machine's dimensions:
The machine has a high of feeder of 900mm, which is quite high. The power requirement is 4Kw, which is relatively high as well. The weight of the machine is 2300kgs, which is quite heavy. The speed of the machine is 60m/min, which is fast.
Spare Parts
Spare parts are essential for maintaining and upgrading equipment. They can be used to replace worn-out or damaged components, ensuring the machine runs smoothly and efficiently.
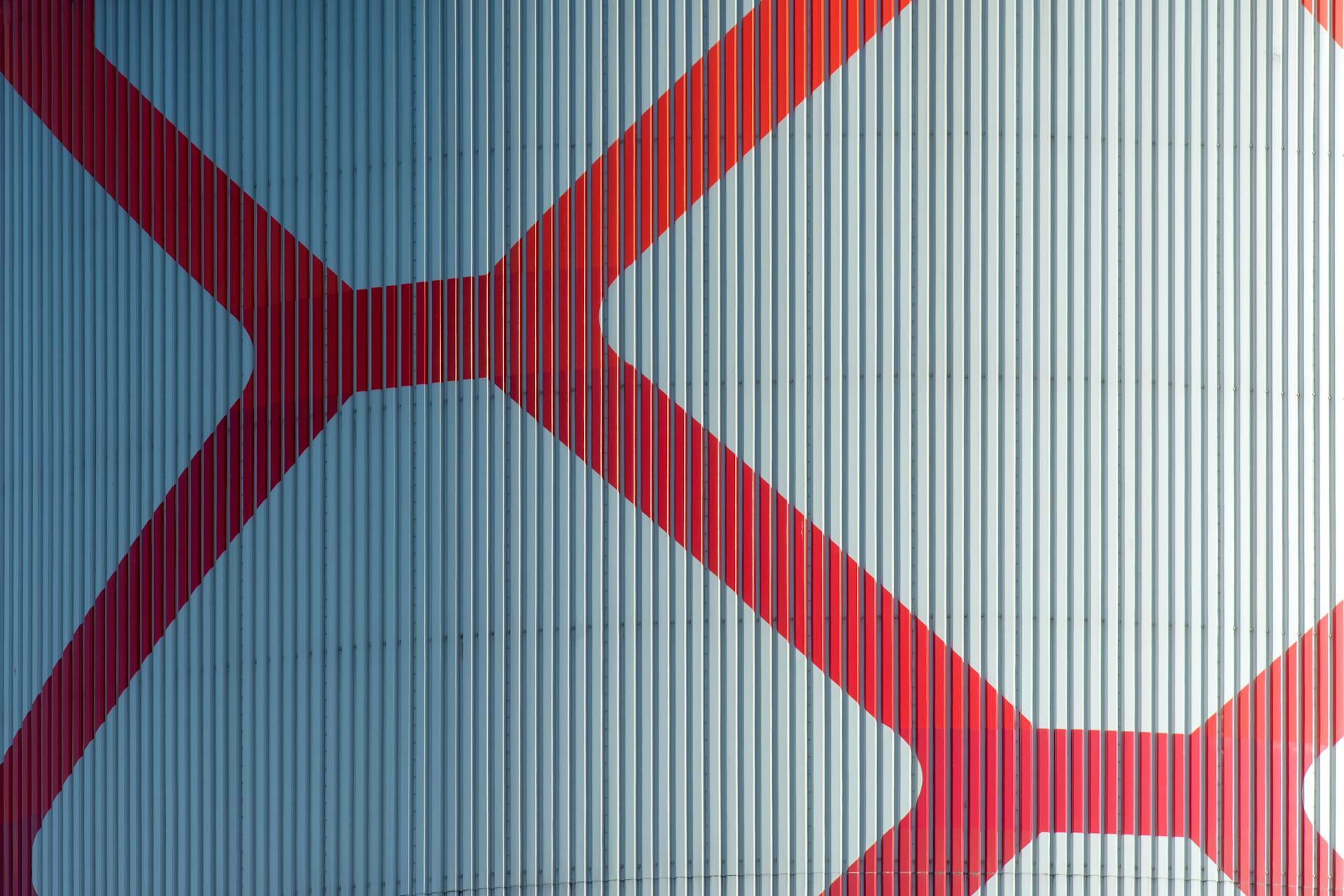
A plastic creasing matrix, for example, is a crucial spare part that helps maintain the integrity of corrugated sheets. It's a vital component in the production process.
Handle hole attachments are another important spare part that ensures secure and stable operation of equipment. They prevent loose attachments that can cause damage or malfunction.
Pushers for corrugated sheets are also a vital spare part that helps in the production process. They are designed to efficiently push the corrugated sheet through the machine, minimizing downtime and increasing productivity.
Here's a list of some common spare parts:
- Plastic Creasing Matrix
- Handle Hole Attachment
- Pushers for Corrugated Sheet
- Flexo Printer Slotter CAM Clutch Bearing
- Anvil Cover (HB9405)
- Flexible pipe for Rotary Joint
Box Making
Box making machines can be fully automatic or semi-automatic. For example, a 5 Ply Fully Automatic Corrugated Box Making Machine is available.
These machines can produce boards with an effective width of 1400 mm-2500 mm. This range can be useful for various box-making applications.
The design speed of semi-automatic box making machines like the Super Nataraja model can reach up to 250 m/min.
Expand your knowledge: Semi-automatic Bag in Box Filling Machines
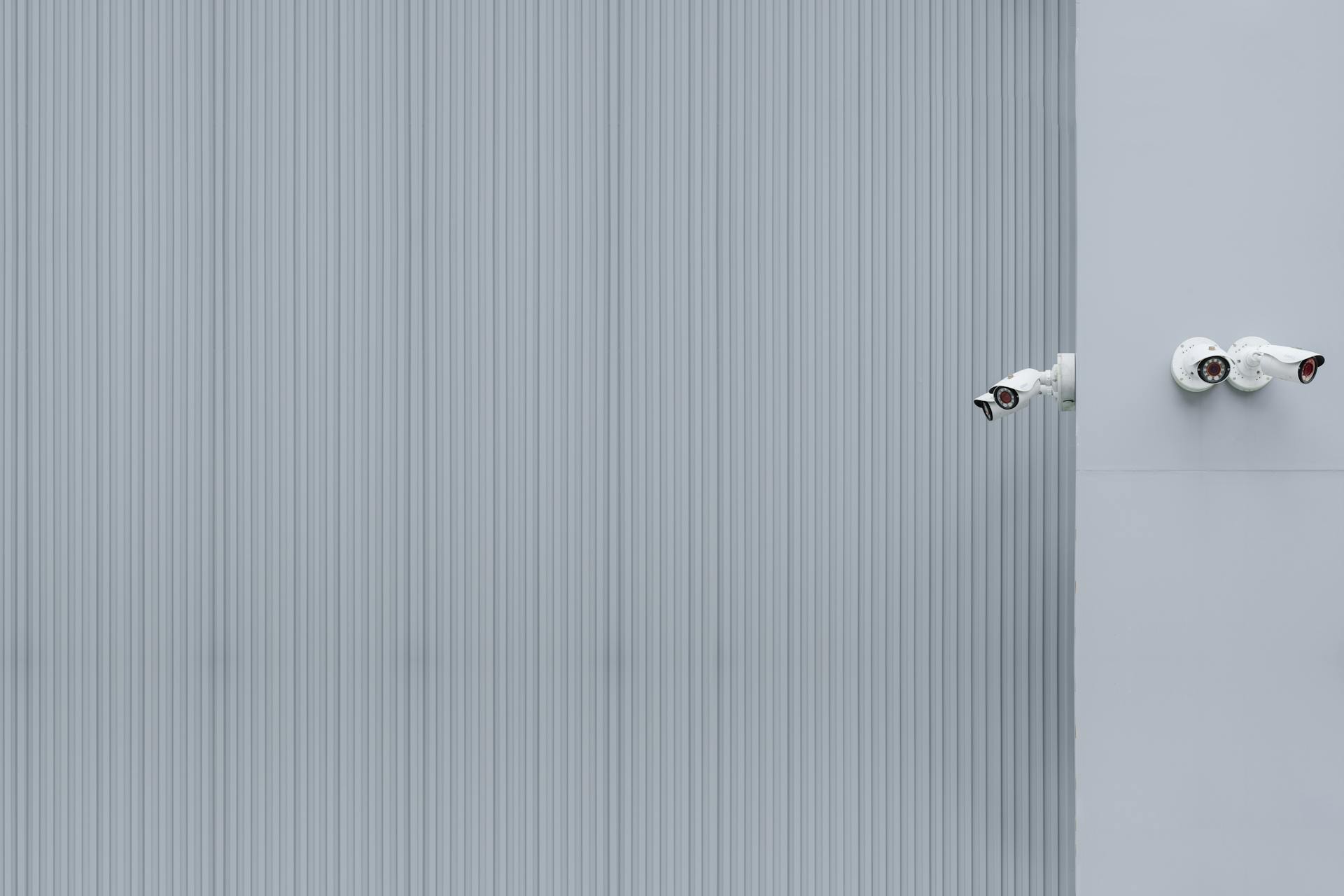
Automatic change orders can be made in as little as 5 seconds on some machines. This feature can significantly improve production efficiency.
A semi-automatic box making machine, like the Super Nataraja model, can be synchronized with a production management control system. This allows for automatic change orders at high speeds.
During operation, the waste paperboard can be minimized to less than 700mm due to the automatic change order feature.
Scrap Bailing
Scrap bailing is a crucial process in recycling, and it's interesting to see the different machines used for it.
A paper scrap bailing machine is a great example, with a double cylinder design that's capable of handling a significant amount of waste.
The dimensions of this machine are quite impressive, with a length of 1.4 tons and a width of 1.3m, making it a compact but efficient piece of equipment.
Its height of 2.8m is also noteworthy, allowing it to be used in various settings.
The machine is capable of producing a paper bag that weighs about 260 kg.
1800mm Cassette
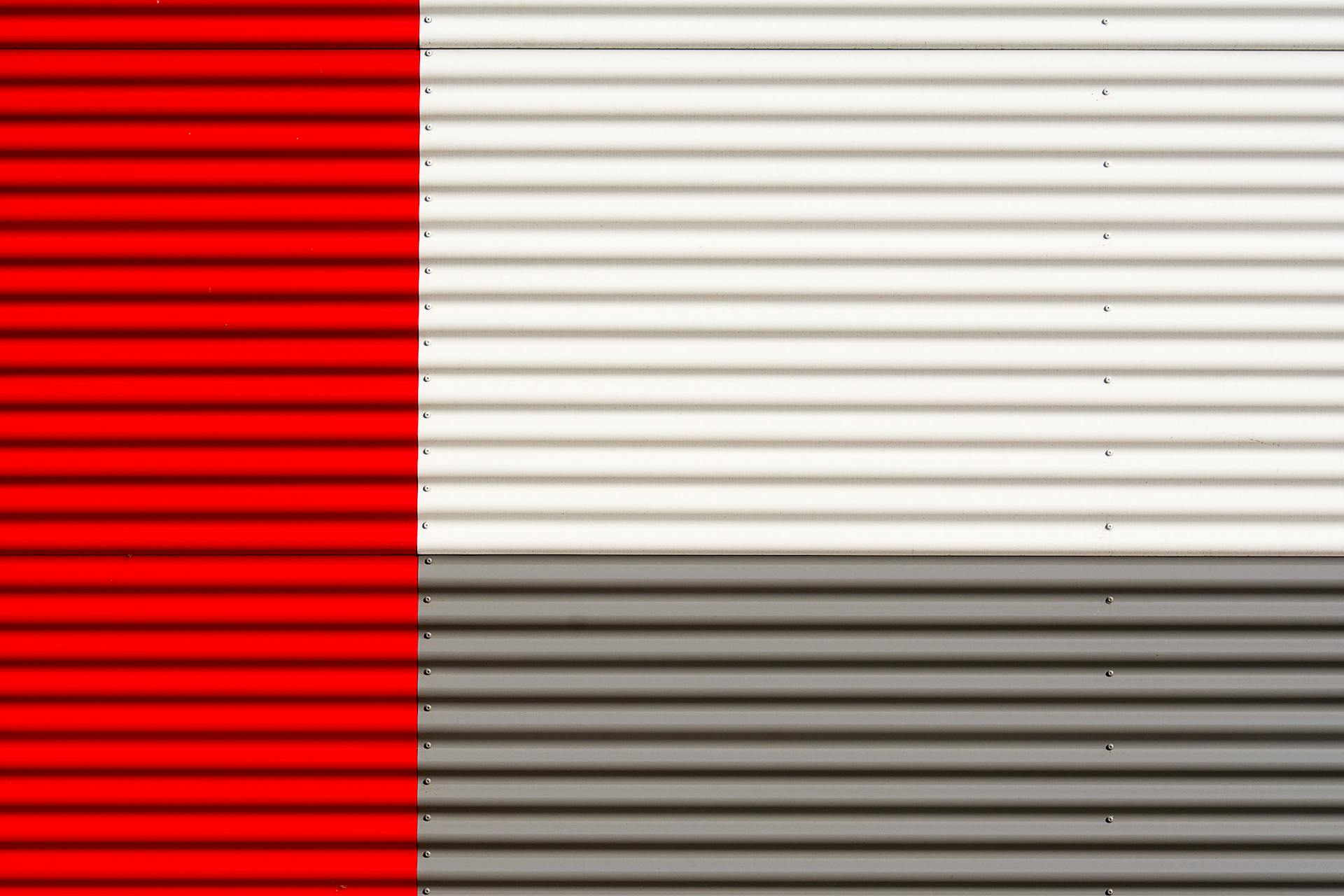
The 1800mm cassette is a common size used in many air conditioning systems, particularly in commercial and industrial settings. It's a popular choice due to its high capacity and reliability.
This cassette type is often used in applications where high airflow rates are required, such as large offices or retail spaces. Its dimensions are 1800mm wide and 300mm deep, making it a compact yet effective solution.
The 1800mm cassette is typically paired with a corresponding outdoor unit, which is usually a larger and more powerful device. This combination provides a high cooling capacity of up to 24,000 BTUs.
Nagpal
Nagpal is a renowned manufacturer of corrugating machinery, with a wide range of products designed for various applications.
Their machinery is capable of producing 5000 boxes per day, with a speed of 40 meters per minute.
The Nagpal Natraj Corrugating Machinery Company uses 48 CrMo high-quality alloy steel in their construction, ensuring durability and reliability.
Their machines are equipped with advanced features such as anti-deviation wide belt conveying, which provides stability and good order.
The Nagpal Fingerless Corrugation Machine has a capacity of 6 tonnes per shift and operates at a speed of 40 meters per minute.
Nagpal's machines are designed to cater to the ever-changing requirements of their clients, with features such as vacuum suction and groove-free glue applicator.
The NAGPAL High Speed Fingerless Corrugation Machine has a speed of 150 meters per minute and a capacity of 10 tonnes per day.
Here are some specifications of Nagpal's machines:
Nagpal's machines are designed to be automatic, with features such as automatic grade and hydraulic reel stand horsepower.
Manufacturing and Production
Corrugated cardboard production lines are available in various models, including the WJ150, WJ180, WJ200, and WJ260.
These lines can produce high-quality corrugated cardboard with capacities ranging from 8 to 10 tons per day.
The NATRAJ CORRUGATING MACHINERY COMPANY offers a 7 Layer Automatic corrugated board plant with a production capacity of 8-10 tons per day.
Here are some key specifications of the NATRAJ CORRUGATING MACHINERY COMPANY's 7 Layer Automatic corrugated board plant:
- Capacity: 8-10 tons per day
- No. of Ply: 3 Ply
- Speed: 80 mtr/p/m
High Speed

High speed manufacturing is all about efficiency and speed. High Speed Single Face Corrugation Machines can produce 1-3 Ton/day of corrugated sheets.
These machines are designed to operate at a frequency of 50/60 Hz and a voltage of 220 V, making them suitable for various industrial applications. They also have a max working width of 1600 mm and a working air pressure of 0.6-0.9 Mpa.
The economy speed of these machines is 60 m/min, while the design speed is 80 m/min. This means they can produce corrugated sheets at a rate of up to 80 meters per minute.
Here are some key features of high speed corrugation machines:
- Automatic grade: Automatic
- Drive reducer box: Oil immersed type lubricating to reduce noise and keep running stable
- Corrugating roller, pressure roller, and glue roller adjustment: Pneumatic adjustment
- Bearing of corrugated and pressure roller: High temperature lubricate grease
- Glue parts: Auto supply glue circularly
Some high speed corrugation machines are designed to produce 2 ply corrugated sheets at a speed of 150 meters/min. These machines have a hydraulic reel stand with a 5.hp motor and can produce up to 10 tonnes per day.
Here are some specifications of a high speed fingerless corrugation machine:
Automatic 5 Ply Board Line
The Automatic 5 Ply Board Line is a game-changer for manufacturers who want to streamline their production process. This line includes a 5 Ply Fully Automatic Corrugated Box Making Machine, which can produce boxes quickly and efficiently.
One of the key components of this line is the Down Stacker, which is designed for use in automatic corrugated board plants. This machine helps to speed up production and reduce labor costs.
If you're in the market for a refurbished 5 Ply Corrugated Board Plant, the JS 1800mm model is a great option to consider. It's a reliable and cost-effective choice that can help you get started with your production line.
Here are some of the key features of the Automatic 5 Ply Board Line:
- 5 Ply Fully Automatic Corrugated Box Making Machine
- Down Stacker For Automatic Corrugated Board Plant
- Refurbished JS 1800mm 5 Ply Corrugated Board Plant
Frequently Asked Questions
What is the cost of 42 inch corrugation machine?
The cost of a 42 inch corrugation machine is ₹ 650,000 per unit. This price includes a semi-automatic automation grade machine with a capacity of 30-35 meters per minute.
What machine is used to make corrugated cardboard?
The corrugator machine is used to manufacture corrugated cardboard by sandwiching a fluted sheet between two flat sheets. This machine plays a crucial role in producing cardboard, a widely used material in packaging and shipping.
What is the difference between kraft paper and corrugated paper?
Kraft paper is ideal for industries seeking cost-effective and eco-friendly solutions, while corrugated paper is preferred for its strength and protective qualities. The choice between the two depends on the specific needs of your business or industry.
Sources
- https://www.manoindustrialmachinetools.net/corrugation-machines.html
- https://www.corrugated-line.com/corrugator-machine-corrugated-cardboard-manufacturing-process.html
- https://friendsenggco.com/product/corrugation-machine
- https://www.westriverpackage.com/sale-8558798-cardboard-making-machine-corrugated-paper-preheater.html
- https://dir.indiamart.com/impcat/paper-corrugating-machine.html
- https://www.natrajmachinery.co/semi-automatic-corrugated-box-making-machine.html
Featured Images: pexels.com