
Multi order picking can be a complex and time-consuming process, but with the right tools and strategies, it can be greatly improved.
According to recent studies, implementing advanced logistics solutions can increase order picking efficiency by up to 30%.
In a warehouse with a high volume of orders, manual picking can lead to errors and delays, but automated systems can help minimize mistakes and reduce labor costs.
Automated picking systems, such as those using robots or drones, can pick orders up to 50% faster than manual picking methods.
You might like: Order Fulfillment Automation
Introduction
Combining multiple orders onto a single pick list can significantly improve productivity.
This approach reduces the number of trips through the warehouse that warehouse operators have to make, making their job more efficient.
By assigning a specific bin number in the pick order to each order, warehouse operators can easily locate the items they need to pick.
Warehouse operators can then make a single trip through the warehouse with a picking cart and pick all orders on the pick order at the same time.
This streamlined process can save time and reduce errors, making it a more practical approach to managing multiple orders.
Additional reading: Temu Order Delivery Time
Optimizing Multi Order Picking
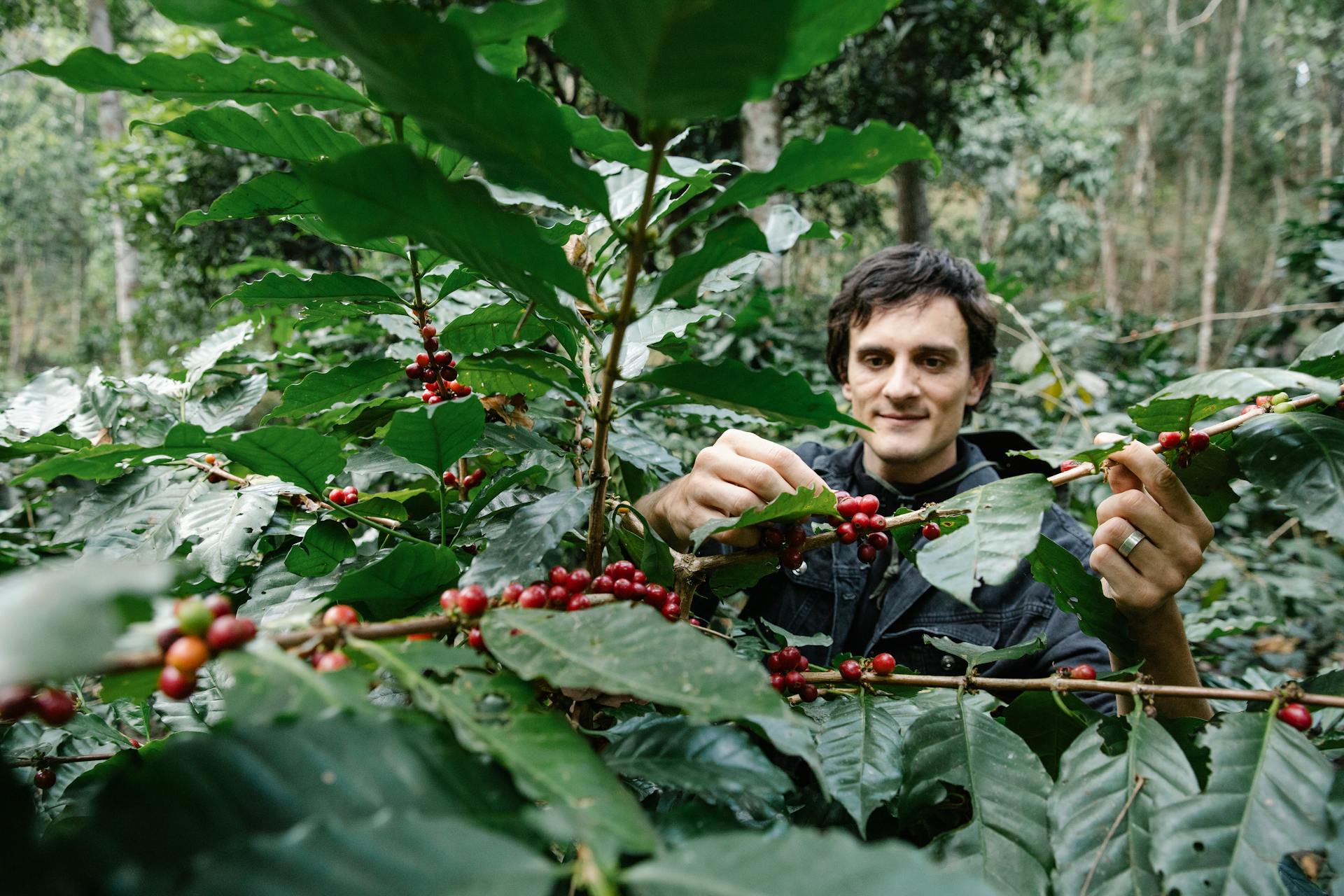
To optimize multi order picking, you need to identify the optimal order picking method, which depends on factors like product range, peak period volumes, and desired delivery times.
The choice between single and multi-order picking can lead to significant differences in efficiency, with multi-order picking aiming to minimize travel distances for all order pickers.
By picking all items for several orders on a single route, or by picking the total quantity of one specific SKU for several customers at the same time, multi-order picking can be more efficient.
However, with multi-order picking, all picked items must be assigned to the right customer orders in an intelligent manner, which can be done during order picking by using check numbers or colour codes.
The efficiency boost that can be achieved with multi-order picking depends on the product range, the number of SKUs per order, the number of order pickers, and the warehouse size.
If splitting the items after picking takes too much time or leads to errors, the potential efficiency improvement drops, or the delivery reliability suffers.
If this caught your attention, see: Multi Channel Fulfillment Order
Process Analysis and Business Logic
To understand the benefits of multi-order picking, it's essential to analyze the current order handling and picking processes. Key questions to ask include: What are the current travel distances of all order pickers, and how many packages per hour do they pick on average?
For many small, individual orders, multi-order picking might not be worthwhile due to expected delivery times, such as same-day delivery. However, businesses with larger warehouses and dozens of order pickers can usually recover an investment in multi-order picking within a short timescale.
The existing ERP and/or WCS/WMS system's capability to support multi-order picking is a crucial consideration. If the system doesn't have this capability, an additional business logic layer may be needed for quantity calculations and adjustments to voice dialogue.
A good example of successful multi-order picking implementation is A.S. Watson, a Dutch market leader in health & beauty. They achieved an impressive 38% improvement in efficiency by combining orders and minimizing travel distances.
Explore further: Order and Delivery Management System
Here are some key questions to ask when analyzing order handling and picking processes:
- What are the current travel distances of all order pickers, and how many packages per hour do they pick on average?
- Is the product range or part of the range suitable for item-based or order-based multi-order picking, and does that fit within the time windows available for order picking?
Automating the creation of pick orders can also help streamline the process, especially for large numbers of orders. This can be done through logic such as selecting a certain number of orders and pressing "Create pick order", which can result in multiple pick orders being created.
Technology and Solution
In multi order picking, automation can significantly reduce picking errors by as much as 70% and increase productivity by up to 30%.
With the help of warehouse management systems, pickers can receive real-time updates on order status and location of items, reducing search time and increasing efficiency.
Automated guided vehicles can navigate through warehouses with ease, reducing travel time and increasing productivity by up to 20%.
RFID technology can accurately track inventory levels and detect any discrepancies, reducing stockouts and overstocking by up to 15%.
Implementing a zone picking system can reduce travel time and increase productivity by up to 25% by allowing pickers to focus on a specific zone at a time.
Investing in a warehouse management system can also help to reduce labor costs by up to 10% by streamlining processes and reducing the need for manual data entry.
A different take: Order Fulfillment in Supply Chain Management
Implementation and Demo
Visitors can experience the latest picking technologies firsthand at our Solution Center, where they can even use their own order data in a simulated environment.
Our engineers can set up a test drive environment using a sample of your actual order data, giving you a real-world look at how our system works.
You can also meet us at Booth 1543 at NA 2010 in Cleveland, where we'll be offering demonstrations of our system in action.
We'll be showcasing one order downloaded to Lightning Pick Version 6.0, and then walking it through pick-to-light, low-volume pick-to-light, RF, and voice picking areas.
You can view live productivity data on our LP News large format LED 'scoreboard' message displays during the demo.
Here's an interesting read: Order Fulfillment System
Editing
Editing is a crucial part of multi-order picking. You can edit a pick order by going to Warehouse ⇒ Pick orders and clicking on the one you want to modify.
To add or remove orders from a pick order, you'll see a screen with two sides: the right-hand side contains all the orders currently in the pick order, while the left-hand side shows all other available orders.
The >> button is used to add orders to the pick order, and the << button is used to remove them. This makes it easy to adjust your pick order as needed.
Additional reading: All Pallets Side Order
Printing the Combined List
Printing the Combined List is a crucial step in multi order picking. You can do this by selecting any order in the order list and then printing the Pick list (pick order).
The pick list is ordered by location, so you only have to visit each location once. This is especially helpful when you're picking multiple orders.
Frequently Asked Questions
What are the types of order picking?
There are 8 types of order picking methods used in warehouses, including Single Order Picking, Batch Picking, and others, each with its own efficiency and application. Understanding these methods can help optimize warehouse operations and improve order fulfillment.
What is batch order picking?
Batch order picking involves a single picker picking multiple orders at once to optimize pick paths and reduce duplicate visits to item locations. This efficient method streamlines warehouse operations and improves order fulfillment.
Sources
- https://docs.oracle.com/en/cloud/saas/netsuite/ns-online-help/section_161618492327.html
- https://www.zetes.com/en/warehouse-solutions/order-picking/logistics-optimisation-through-the-use-of-multi-order-picking
- https://docs.ongoingwarehouse.com/manuals/picking-multiple-orders-at-the-same-time
- https://ixtenso.com/sustainability/logistics-optimisation-through-the-use-of-multi-order-picking.html
- https://lightningpick.com/multimodal-order-picking-solutions/
Featured Images: pexels.com