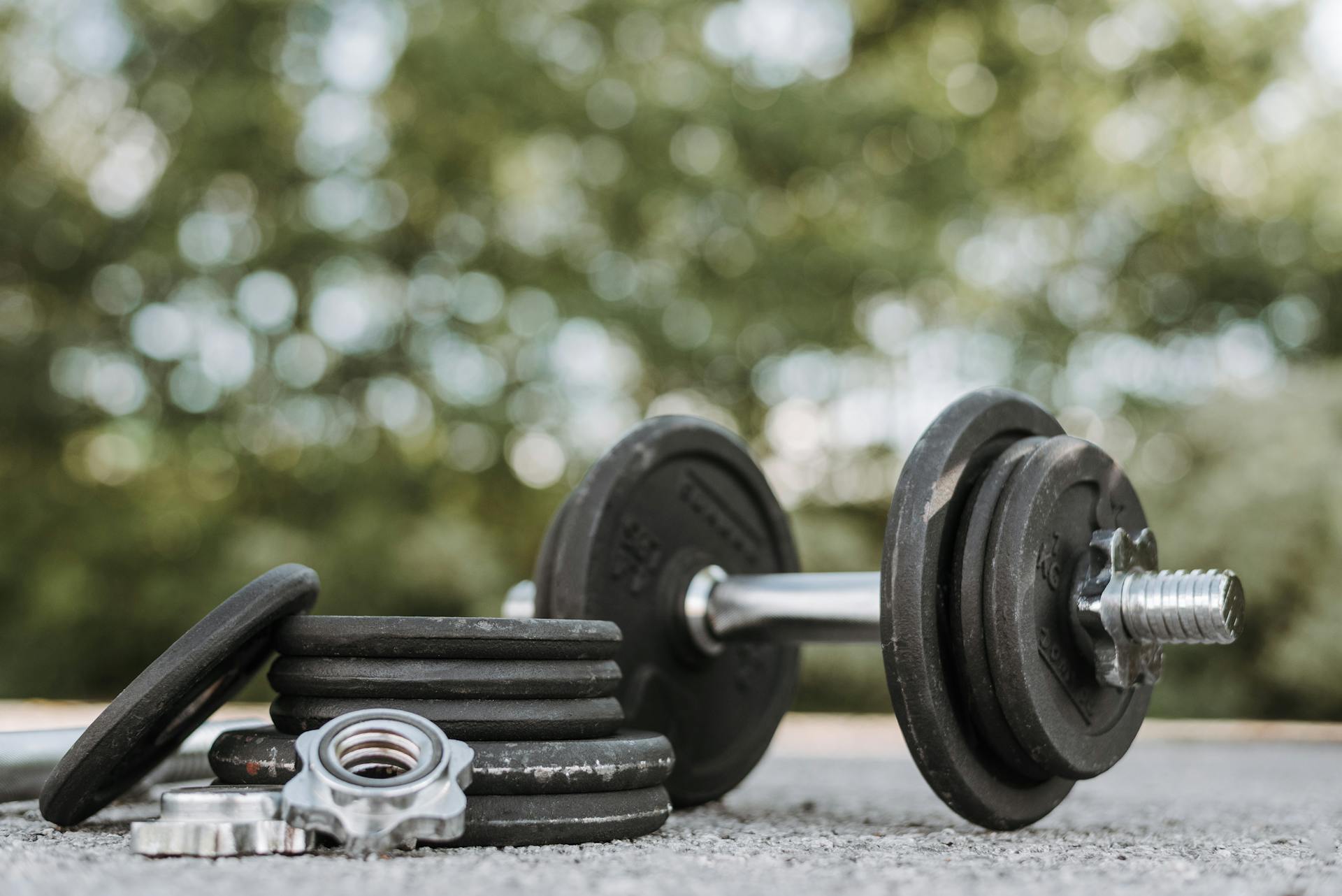
Loading dock plates are a crucial component of efficient warehouse operations. They provide a safe and durable surface for loading and unloading heavy equipment and materials.
A well-designed loading dock plate can last up to 10 years with proper maintenance. This can save warehouses a significant amount of money in the long run.
Loading dock plates come in different materials, including steel and aluminum. Steel plates are more durable and can withstand heavy loads, while aluminum plates are lighter and more corrosion-resistant.
Properly maintained loading dock plates can reduce the risk of accidents and injuries by 50%. This is especially important in warehouses where heavy equipment and materials are constantly being moved.
Additional reading: Loading Bay Equipment
Types of Dock Plates
There are several types of dock plates available, each designed for specific applications. Aluminum dock plates are relatively lightweight, making them easy to move with handles, and are suitable for lighter equipment such as hand carts and pallet jacks.
Dock plates feature locking legs to prevent shifting out of place while in use. Steel dock boards, on the other hand, are designed for heavy capacity loading dock applications with capacities ranging from 10,000 to 30,000 lbs.
Some dock plates are designed for non-powered equipment and are suitable for low-budget, lower volume loading environments. Others, like the BBTA, feature lightweight aluminum construction and locking legs for safe loading and unloading procedures, and are available in capacities from 5,000 to 20,000 lbs.
What's the Difference?
So, you're wondering what the difference is between dock plates and dock boards? Well, let's break it down. Dock plates are typically flat and simple, designed to bridge small gaps, and are suitable for light to moderate loads.
They're often manually positioned and used in applications where smaller loads or frequent repositioning are involved. For example, the Beacon brand Dock Plate is designed for lighter equipment such as hand carts, pallet jacks, and foot traffic.
On the other hand, dock boards are larger and more robust than dock plates. They feature reinforced curbs, anti-slip surfaces, and safety chains to ensure secure movement between the dock and the vehicle. This makes them ideal for heavy-duty applications, like the Steel Dock Board designed for heavy capacity loading dock applications with capacities ranging from 10,000 to 30,000 lbs.
Here's a quick comparison of the two:
For instance, the BBTA features a lightweight aluminum construction with locking legs, making it suitable for lighter loads, while the BTS features beveled edges and diamond-plating for safe and efficient use in heavy-duty applications with capacities up to 30,000 lb.
Boards
Aluminum dock boards are a popular choice for loading applications, offering a lightweight yet sturdy alternative to steel dock boards. They provide excellent strength-to-weight ratios, making them ideal for applications where portability and ease of handling are essential.
Aluminum dock boards can support capacities of up to 15,000 Lbs, making them suitable for low to medium volume dock loading applications. They're also resistant to corrosion, making them a great option for outdoor use or in environments exposed to moisture or chemicals.
If you need to load hand trucks and dollies, aluminum dock boards are an ideal solution. They're designed to provide a smooth and stable surface for these types of vehicles.
When choosing a loading dock board, consider the load capacity and ensure it can support the maximum weight your dock will need to handle. This will help prevent accidents and ensure the board's durability.
Here are some key factors to consider when selecting a loading dock board:
- Load Capacity: Determine the maximum weight the dock board needs to support.
- Vehicle Compatibility: Assess the types of vehicles that will be using the dock board.
- Safety Features: Evaluate the safety features necessary for your application.
- Adjustability: Consider adjustable dock boards with flexible leg or lip extensions.
- Portability: Opt for portable dock boards that are lightweight and equipped with handles.
Characteristics and Benefits
Loading dock plates are designed to provide a smooth and durable surface for loading and unloading heavy equipment and materials.
They can be made from a variety of materials, including rubber, steel, and aluminum, to suit different load capacities and environments.
Rubber dock plates are particularly effective at reducing the impact of heavy loads on the dock surface, which can help prevent damage and extend the lifespan of the dock.
Steel dock plates are often used in heavy-duty applications, such as warehouses and manufacturing facilities, where high load capacities are required.
A unique perspective: Oversize Load
Aluminum dock plates are lightweight and corrosion-resistant, making them a good choice for outdoor use or in areas with high humidity.
Dock plates can also be equipped with features such as non-slip surfaces, which can improve safety by reducing the risk of slipping and falling.
Non-slip surfaces can be particularly important in areas with high foot traffic or where equipment is being loaded and unloaded frequently.
Overall, loading dock plates are an essential component of any loading dock operation, providing a safe and efficient way to load and unload heavy equipment and materials.
See what others are reading: Loading Dock Safety Equipment
Dock Plate Applications and Benefits
Warehouses with high volumes of incoming and outgoing goods greatly benefit from dock plates, which optimize workflow and increase productivity.
Dock plates provide a smooth transition between the warehouse and transportation vehicles, reducing downtime and streamlining operations. This is especially true for warehouses that handle a high volume of goods.
Warehouses can install dock plates to improve the efficiency of their operations. By doing so, they can reduce the time and effort required to load and unload goods.
Dock plates facilitate quick and efficient loading and unloading, making them an invaluable asset for warehouses. They ensure that goods are moved safely and efficiently, minimizing the risk of accidents.
Warehouses can benefit from installing dock plates to accommodate different vehicle heights and configurations. This allows for efficient loading and unloading across various transportation vehicles.
Choosing the Right Dock Plate
Choosing the right dock plate is crucial to ensure safe and efficient material handling processes. Load capacity is a key factor to consider, as it determines the maximum weight the dock plate needs to support.
To determine the load capacity, you need to consider both the static load (when the load is stationary) and the dynamic load (when the load is in motion). This will help ensure the dock plate's durability and safety.
Vehicle compatibility is also essential, as it affects the dock plate's dimensions, weight capacity, and surface materials. You should consider the types of vehicles that will be using the dock plate and ensure that it can support their size, weight, and wheel configuration.
A fresh viewpoint: Wide Load vs Oversize Load
Here are some essential considerations to keep in mind when choosing a dock plate:
- Load Capacity: Determine the maximum weight your dock plate needs to support.
- Vehicle Compatibility: Consider the types of vehicles that will be using the dock plate.
- Environment: Evaluate the environmental conditions in which the dock plate will be used.
- Safety Features: Assess the safety features necessary for your specific application.
- Ergonomics: Consider the ease of use and maneuverability of the dock plate.
Cost-Effectiveness
Steel dock plates and boards might have a higher initial cost than aluminum, but they often pay off in the long run due to their durability and longer lifespan.
Their ability to withstand heavy use and last longer means you'll need to replace them less often, which can save you money in the long term.
For applications that require higher weight capacities, steel dock plates and boards can be more cost-effective than aluminum.
A different take: How Much Does It Cost to Build a Loading Dock
Key Factors for Choosing
Choosing the right dock plate for your needs requires careful consideration of several key factors.
Load capacity is a crucial aspect to determine the maximum weight your dock plate needs to support. Both static and dynamic loads should be considered to ensure the dock plate's durability and safety.
Vehicle compatibility is essential to assess the types of vehicles that will be using the dock plate. Ensure that the dock plate dimensions, weight capacity, and surface materials are suitable for the vehicles' size, weight, and wheel configuration.
Environmental conditions, such as moisture, temperature variations, and corrosive substances, can impact the choice of material. Different dock plate materials offer varying degrees of resistance to these elements.
Safety features, such as curbs, non-slip surfaces, or integrated handles, can be necessary for your specific application. Consider selecting dock plates that offer these options to enhance safety.
Ergonomics is also an important consideration to ensure the ease of use and maneuverability of the dock plate. If your operation involves frequent repositioning or portability, opt for lightweight or portable dock plates that can be easily handled and transported.
Here are some key factors to consider when choosing a dock plate:
- Load capacity
- Vehicle compatibility
- Environmental conditions
- Safety features
- Ergonomics
By carefully assessing these factors, you can select a dock plate that meets your operational requirements, enhances safety, and improves overall efficiency.
Dock Plate Features and Options
Steel dock plates and boards are incredibly versatile, suitable for use in both outdoor and indoor settings. They're strong and durable, making them perfect for a wide range of applications.
Heavy-duty dock plates are a must-have for facilities dealing with heavy loads and equipment. These robust structures can withstand significant weights and endure the demanding nature of industrial environments.
Their ability to handle heavy loads with ease ensures the safe and efficient movement of heavy equipment, preventing structural damage and optimizing material handling operations.
Versatility
Steel dock plates and boards can be used in a variety of environments, including outdoor and indoor settings. They're a great option for warehouses, factories, and even construction sites.
Their strength and durability make them suitable for a wide range of applications, from heavy-duty equipment to forklift traffic. This versatility is one of the reasons they're so popular among businesses.
Whether you're working with heavy machinery or need to create a safe path for pedestrians, steel dock plates and boards can get the job done.
Dock Plate Features and Options
Dock plates come in various capacities, ranging from 15,000 to 90,000 pounds.
These capacities are suitable for different types of operations, from small to large-scale material handling.
Heavy-duty dock plates are designed to withstand significant weights and endure demanding industrial environments.
They ensure the safe and efficient movement of heavy loads, preventing structural damage and optimizing material handling operations.
For heavy loads, it's recommended to use heavy-duty dock plates or loading dock boards specifically designed to handle robust weights.
These heavy-duty options provide the necessary strength and stability required for heavy load applications.
Some dock plates are designed specifically for forklifts, providing a secure transition between the dock and the forklift.
They allow for seamless movement of goods and are engineered to handle the weight and impact associated with forklift operations.
These dock plates are essential for streamlining material handling operations and enhancing the efficiency and functionality of forklifts.
They are designed to handle light to moderate loads, but heavy-duty options are available for heavy loads.
Heavy-duty dock plates are indispensable in facilities dealing with heavy loads and equipment.
Related reading: Loading Dock Ramps for Forklift
Dock Plate Materials and Construction
Steel dock plates are renowned for their exceptional strength and durability, making them suitable for heavy-duty applications. They can withstand the weight and impact associated with forklifts, pallet jacks, and other industrial equipment.
Steel dock boards are designed to handle significant loads and endure the rigors of frequent forklift and equipment traffic. They often feature reinforced curbs, anti-slip surfaces, and safety chains to ensure secure movement between the dock and the vehicle.
Steel is inherently stronger and more durable than aluminum, making steel dock plates and boards better suited for heavy-duty applications and high-traffic environments.
Dock Plate Materials and Construction
Steel is the material of choice for dock plates and boards, renowned for their exceptional strength and durability. This makes them suitable for heavy-duty applications and high-traffic environments.
Steel dock plates and boards can handle significant loads, with capacities ranging from 10,000 to 40,000 Lbs. They are designed to withstand the impact of forklifts and equipment, ensuring a safe transition between the dock and the vehicle.
Steel is inherently stronger and more durable than aluminum, making it better suited for heavy-duty applications. This is due to its resistance to bending, warping, or other forms of damage.
Steel dock plates and boards often feature reinforced curbs, anti-slip surfaces, and safety chains to ensure secure movement between the dock and the vehicle. This attention to detail provides a safe and reliable solution for loading and unloading shipments.
Aluminum dock plates, on the other hand, are ideal for low to medium volume loading dock applications. They offer a lighter and more cost-effective solution, but may not be suitable for high-traffic environments.
Steel dock plates and boards provide long-lasting solutions, reducing the need for frequent replacements and minimizing downtime. This is a significant advantage in industrial settings where efficiency and productivity are paramount.
Plastic
Plastic dock plates are a lightweight and cost-effective alternative to traditional metal options. They're suitable for light to moderate loads.
In environments where corrosion resistance is essential, plastic dock plates are a great choice. Moisture can cause damage to metal surfaces, but plastic dock plates can withstand wet or humid conditions.
Dock Plate Safety and Maintenance
Loading dock plates play a vital role in warehouse operations, improving efficiency and safety by bridging the gap between the dock and the transportation vehicle.
Effective loading dock plates can keep your employees more secure and efficient in their everyday tasks, as mentioned by the Occupational Safety and Health Administration (OSHA) in its guide to forklift operations.
To ensure safety, it's essential to use vehicle restraint systems, such as wheel chocks, to secure trucks and trailers. Integrated systems directly into the dock are superior from a safety perspective.
Sufficient anchors for dock plates are also crucial, as they prevent the plates from sliding while people or vehicles are on them. This makes the loading and unloading process safer and more efficient.
Regular maintenance is key to preventing unplanned downtime and delays. By focusing on proactive maintenance and emergency repair, you can deliver a better experience for your employees and improve your overall supply chain performance.
You might enjoy: Loading Dock Systems
Low Maintenance
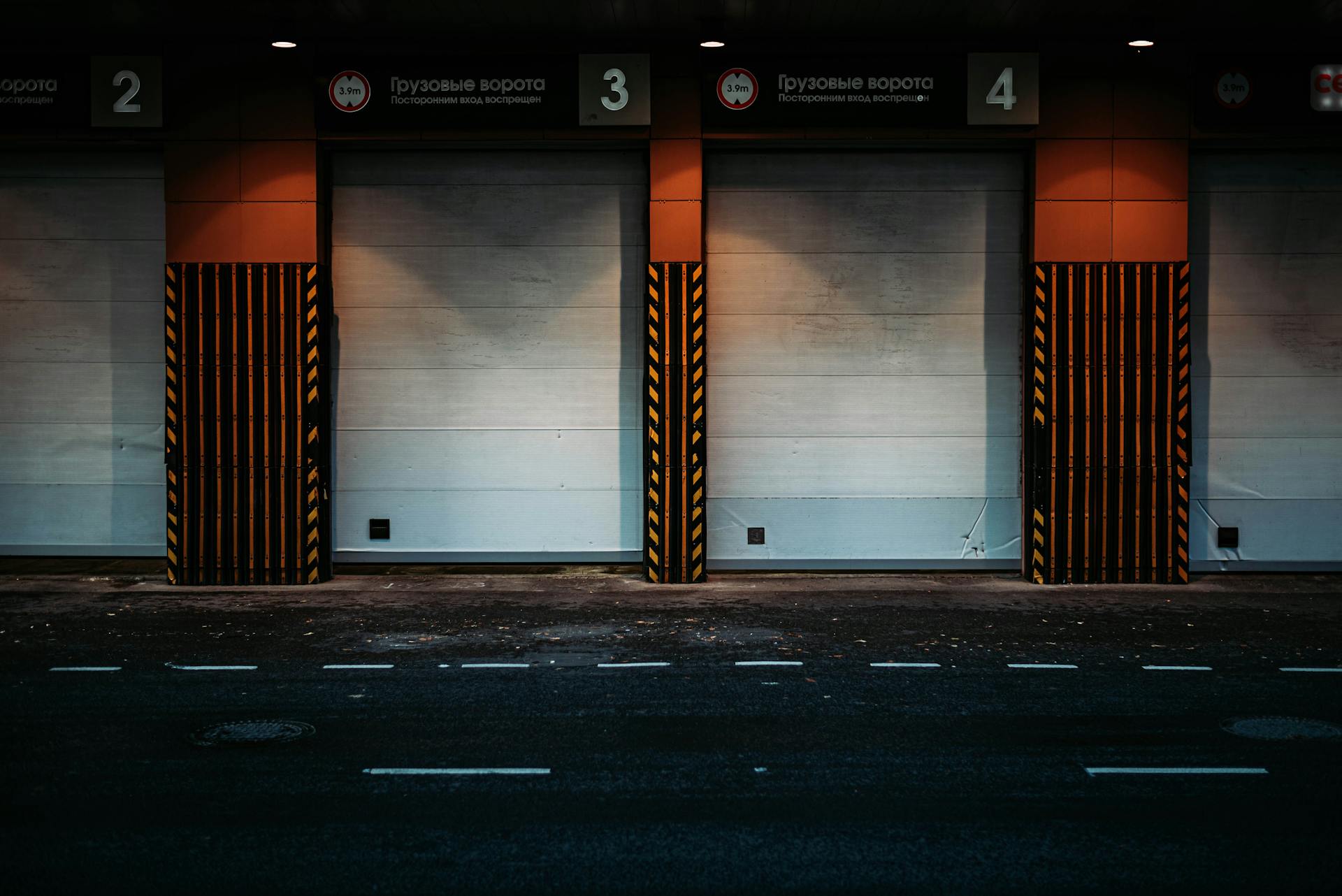
Aluminum dock plates and boards require minimal maintenance due to their corrosion resistance.
This means they don't need to be painted or coated to protect against rust, which reduces the need for ongoing maintenance and associated costs.
In fact, their low maintenance needs are a significant advantage over steel dock plates and boards.
By choosing aluminum dock plates and boards, you can save time and money on maintenance tasks.
Their durable design also helps to minimize the risk of equipment failure, which can cause delays and disruptions in your operations.
You might like: Loading Dock Maintenance
Safety Impact
Effective loading dock plates can keep your employees more secure and efficient in their everyday tasks. The Occupational Safety and Health Administration (OSHA) mentions loading dock plate safety in its guide to forklift operations.
Vehicle restraint systems are a must-have around loading docks, with wheel chocks being the minimum to secure trucks and trailers. Systems integrated directly into the dock are superior from a safety perspective.
You might like: Loading Dock Safety Lights
Using dock plates with sufficient handles is crucial, especially for facilities without mechanical dock levelers, where employees move them into place by hand. These handles should be safe and easy to lift and carry.
Sufficient anchors for dock plates are necessary to prevent them from sliding while people or vehicles are on them. This helps ensure a repeatable and safe process.
As a facility operator, it's essential to ensure all employees are adequately trained in the use of dock plate systems, so they have the knowledge to work safely on these assets, day after day.
Sources
Featured Images: pexels.com