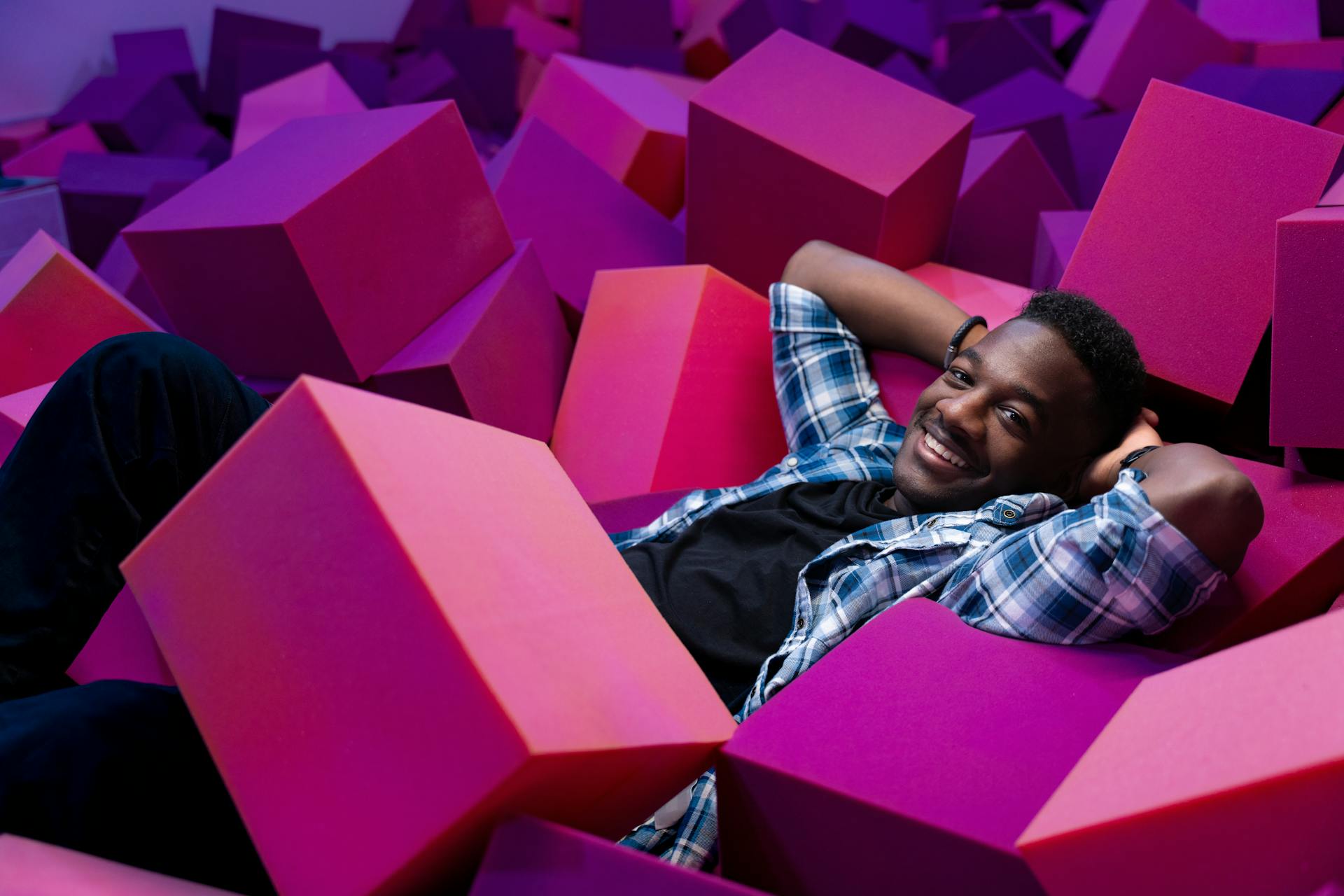
High density polyethylene foam is a type of plastic foam that's incredibly versatile. It's made from a type of plastic called polyethylene, which is a common material used in everything from packaging to pipes.
This type of foam is called "high density" because it's more compact and heavy than other types of foam. It's often used in applications where a lot of support is needed, like in furniture or packaging.
It's also incredibly durable and resistant to wear and tear. According to the article, high density polyethylene foam has a high compressive strength, making it perfect for applications where it will be subjected to heavy loads.
On a similar theme: High Density Polyethylene Plastic
Characteristics and Types
High density polyethylene foam is a highly valued closed-cell thermoplastic foam substance. It's crafted from numerous compact cells surrounded by solid walls, making it impervious to air, moisture, and chemical penetration.
This design grants polyethylene foam superior strength, density, and rigidity compared to open-cell foams. They are also lightweight and pliable.
Their exceptional impact resistance and durability make them perfect for cushioning purposes. Their minimal thermal conductivity makes them superior insulating materials.
Related reading: Green Cell Foam
Chapter 1: Characteristics
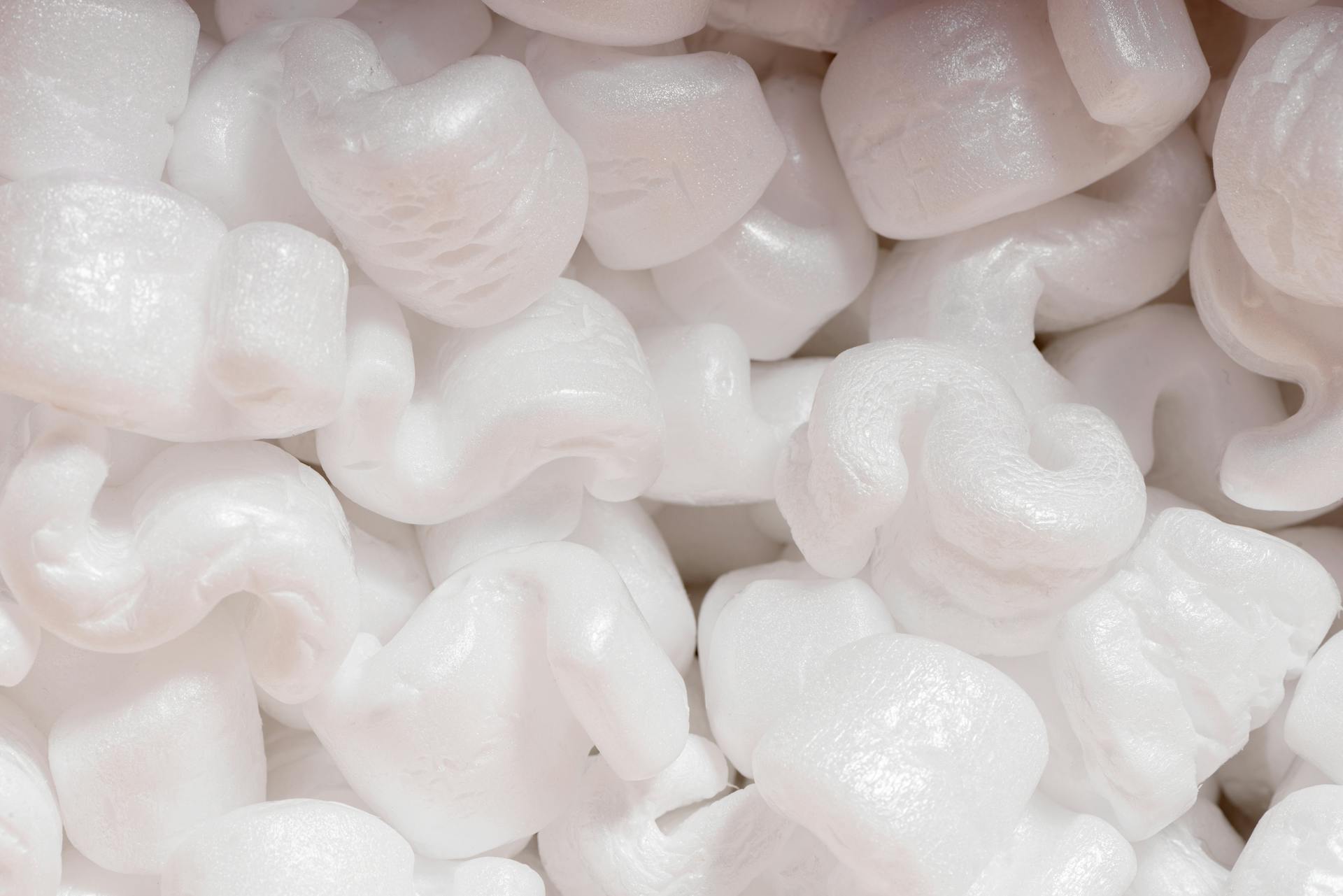
Polyethylene foam is a highly valued closed-cell thermoplastic foam substance.
It's crafted from numerous compact cells surrounded by solid walls, making it impervious to air, moisture, and chemical penetration.
This design grants polyethylene foam superior strength, density, and rigidity compared to open-cell foams.
Polyethylene foam retains its lightweight and pliable qualities despite its closed-cell architecture.
Its minimal thermal conductivity makes it a superior insulating material.
Polyethylene foams are perfect for cushioning purposes due to their exceptional impact resistance and durability.
They exhibit excellent dimensional stability, allowing them to undergo various fabrication techniques.
These foams feature antimicrobial properties that help inhibit bacteria, mold, and other microorganism growth.
Their unique attributes can be further enhanced through combinations with chemical agents or by applying specialized treatments.
Polyethylene foams are characterized by their softness, non-abrasiveness, and resistance to dust, tearing, and decay.
Chapter 2: Types
Polyethylene foams are incredibly versatile materials, and understanding their different types is essential for choosing the right one for your needs.
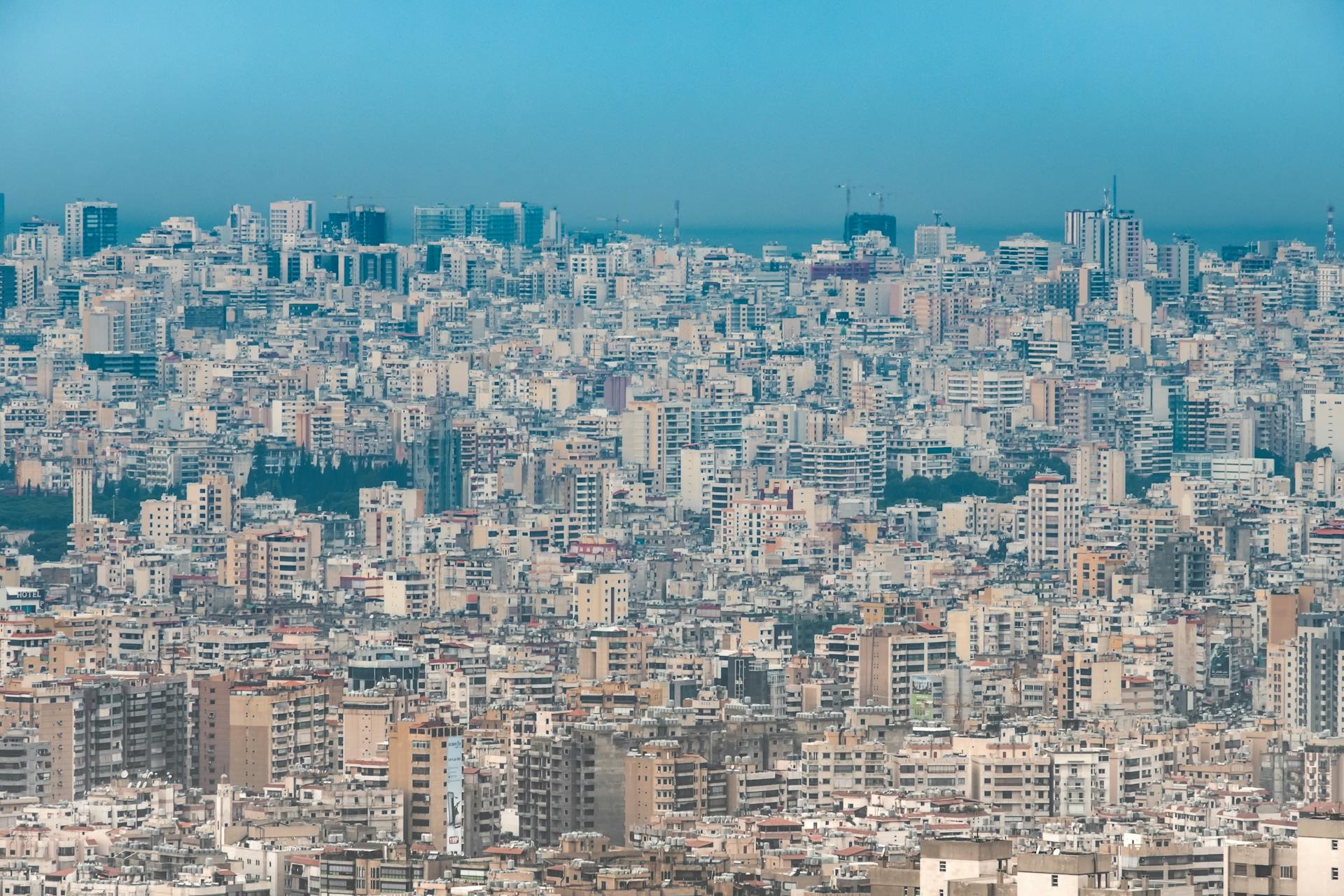
One of the main types of polyethylene foams is cross-linked polyethylene foam, which is known for its high density and excellent resistance to compression.
Another type is expanded polyethylene foam, which is lightweight and has a low density, making it ideal for packaging and cushioning applications.
Polyethylene foams can also be categorized into different grades based on their cell structure, with open-cell foams being more breathable and closed-cell foams being more resistant to moisture.
The type of polyethylene foam you choose will depend on the specific requirements of your project, such as the level of cushioning needed or the amount of weight it will need to support.
High Density
High-density polyethylene foams are preferred for heavy-duty applications due to their high compressive and tensile strength, fatigue resistance, and low thermal shrinkage.
They are used as sport underlays and cushions for shoes and couches, taking advantage of their superior durability and resilience.
High-density polyethylene foams have smaller and thicker cellular walls compared to low-density foams, making them ideal for applications that require more rigidity and support.
Their closed-cell structure efficiently obstructs the flow of liquids and gases, making them impervious to air, moisture, and chemical penetration.
High-density polyethylene foams are also valued for their antimicrobial properties, which help inhibit bacteria, mold, and other microorganism growth.
Here are some of the key characteristics of high-density polyethylene foams:
- High compressive and tensile strength
- Fatigue resistance
- Low thermal shrinkage
- Antimicrobial properties
- Impervious to air, moisture, and chemical penetration
Blowing Agents
Blowing agents are crucial for creating fine cellular structures within the polyethylene matrix. They provide the gas necessary for the foaming process.
There are two main categories of blowing agents: chemical and physical blowing agents. Chemical blowing agents liberate gas through thermal decomposition or a chemical reaction, while physical blowing agents are in a gaseous form.
Some examples of chemical blowing agents include azodicarbonamide, sodium bicarbonate, zinc carbonate, and acylhydrazide. These agents can produce nitrogen or carbon dioxide gas.
Physical blowing agents, on the other hand, are introduced directly into the polyethylene melt. Examples include carbon dioxide, nitrogen, argon, water, air, and chlorofluorocarbons.
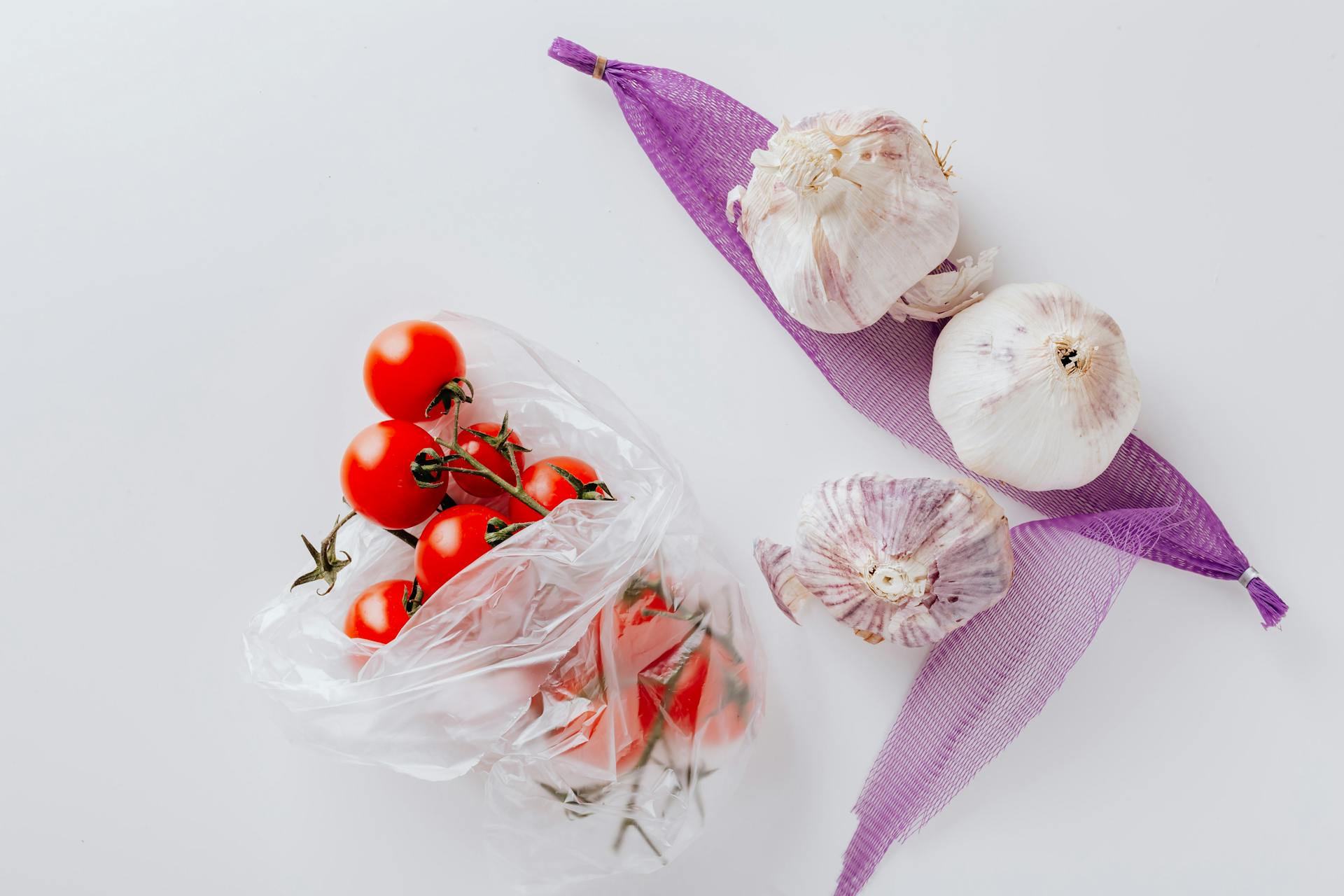
Organic blowing agents can enhance the foaming process by constantly producing dispersible gas and making uniformly-sized bubbles.
Here's a list of some common chemical blowing agents and their characteristics:
- Azodicarbonamide (exothermic)
- Sodium bicarbonate (endothermic)
- Zinc carbonate (endothermic)
- Acylhydrazide (thermal decomposition)
Expandable beads are another type of blowing agent, composed of a thermoplastic acrylic resin polymer with hollow spherical microparticles at their core.
Features and Benefits
High density polyethylene foam is a durable material that can withstand wear and tear, making it suitable for long-term use in various environments.
One of the key benefits of this foam is its versatility, with availability in different thicknesses and densities allowing it to be adapted for numerous uses, from industrial applications to consumer products.
Its closed-cell structure prevents moisture absorption, ensuring it's suitable for both indoor and outdoor applications, which I've personally found to be a major advantage in my own projects.
High density polyethylene foam is also eco-friendly, with many manufacturers now offering recyclable options, making it a sustainable choice for environmentally conscious consumers.
Lightweight yet sturdy, these foam sheets are easy to cut and shape, allowing for hassle-free installation and application.
Here are some key features of high density polyethylene foam:
- Durability: resistant to wear and tear
- Versatility: adaptable for various uses
- Water Resistant: closed-cell structure prevents moisture absorption
- Eco-Friendly: recyclable options available
- Ease of Handling: lightweight yet sturdy
Applications
High density polyethylene foam is a versatile material with a wide range of applications.
It's perfect for packaging fragile items, providing excellent protection during shipping and storage. This is especially useful for electronics and other delicate items.
In construction, these foam sheets are used for insulation and soundproofing, reducing heat loss and improving energy efficiency. They're a great way to make buildings more comfortable and cost-effective.
Their lightweight yet durable nature makes them suitable for use in aircraft interiors and automotive parts, enhancing performance and safety. This is a significant advantage in industries where weight is a critical factor.
High density polyethylene foam is also frequently used in furniture for cushioning, providing comfort without compromising support. This is why you often see it in sofas, chairs, and other upholstered furniture.
Here are some key applications of high density polyethylene foam:
- Packaging: Protecting fragile items during shipping and storage.
- Construction: Insulation and soundproofing for buildings.
- Aerospace and Automotive: Enhancing performance and safety in aircraft interiors and automotive parts.
- Furniture Upholstery: Providing comfort and support in upholstered furniture.
Manufacturing and Materials
High density polyethylene foam is a versatile material that's widely used in various industries. It's made from a type of plastic called polyethylene, which is known for its durability and resistance to wear and tear.
HDPE foam is often used in packaging applications because it provides excellent cushioning and shock absorption properties. This is due to its unique cell structure, which is composed of small, closed cells that absorb impacts and distribute pressure evenly.
In terms of manufacturing, HDPE foam can be produced through various methods, including extrusion and molding. These processes allow for the creation of complex shapes and designs, making HDPE foam a popular choice for custom packaging solutions.
You might enjoy: Packaging Materials Foam Sheets
Resins
Polyethylene resin is the primary component in the production of polyethylene foams.
LDPE (low-density polyethylene) and HDPE (high-density polyethylene) resins are the most commonly used types.
LDPE foams are known for their lightweight and cost-effectiveness.
HDPE foams offer greater strength and durability.
During the foam production process, these resins are melted and combined with agents and additives.
Related reading: Ldpe Foam
Injection Molding
Injection molding is a batch-mode process that can produce foams with complex shapes and precise dimensions. Foam injection molding machines have a barrel with heating zones, a reciprocating screw, and mechanisms for feeding the resin and blowing agent.
The blowing agent is introduced into the polyethylene melt either at the hopper or at a specific point in the barrel. This process can involve significant costs for tooling and energy.
Foam injection molding allows for the production of foams with precise dimensions. The melt is injected with sufficient pressure and speed until it reaches the nozzle, triggering cell nucleation and growth as it fills the mold cavities.
The foam expands to fit the mold, remains in place for a specified time, and is then removed when the mold halves are opened. Any excess material around the foam product is trimmed off.
Suggestion: 40 High Cube Container Dimensions
Machines and Equipment
Polycraftpuf Machine Pvt. Ltd. provides polyethylene foam machinery that supports efficient production, encompassing foam extrusion, shaping, and cutting processes. Their machines offer customizable options for foam thicknesses and densities.
These machines can produce high density polyethylene foam with varying thicknesses and densities, making them suitable for a range of applications.
Polycraftpuf Machine Pvt. Ltd. offers a variety of machines that cater to different production needs, from small-scale to large-scale operations.
Their machines can help increase production efficiency and reduce labor costs, making them a valuable investment for businesses that work with polyethylene foam.
Laminated and Specialized
Polyethylene foam sheets can be laminated with other materials to create thicker layers, enhancing the mechanical strength, cushioning effect, insulation properties, and overall durability of the foam.
This process makes laminated foams incredibly versatile, allowing them to be used in a wide range of applications.
Polyethylene foams can provide comfort and enhance ergonomics, making them perfect for use as padding and cushioning in furniture like chairs, couches, beds, car seats, arm and headrests.
Open-cell foams are softer and more comfortable than polyethylene foams, but polyethylene foams still offer a great balance of comfort and durability.
Sources
- https://www.alibaba.com/showroom/high-density-polyethylene-foam-sheets.html
- https://patents.google.com/patent/WO2002074843A2/en
- https://www.esdgoods.com/high-density-polyethylene-foam.html
- https://www.foamorder.com/foam/cross-poly-foam
- https://www.iqsdirectory.com/articles/foam-fabricating/polyethylene-foam.html
Featured Images: pexels.com