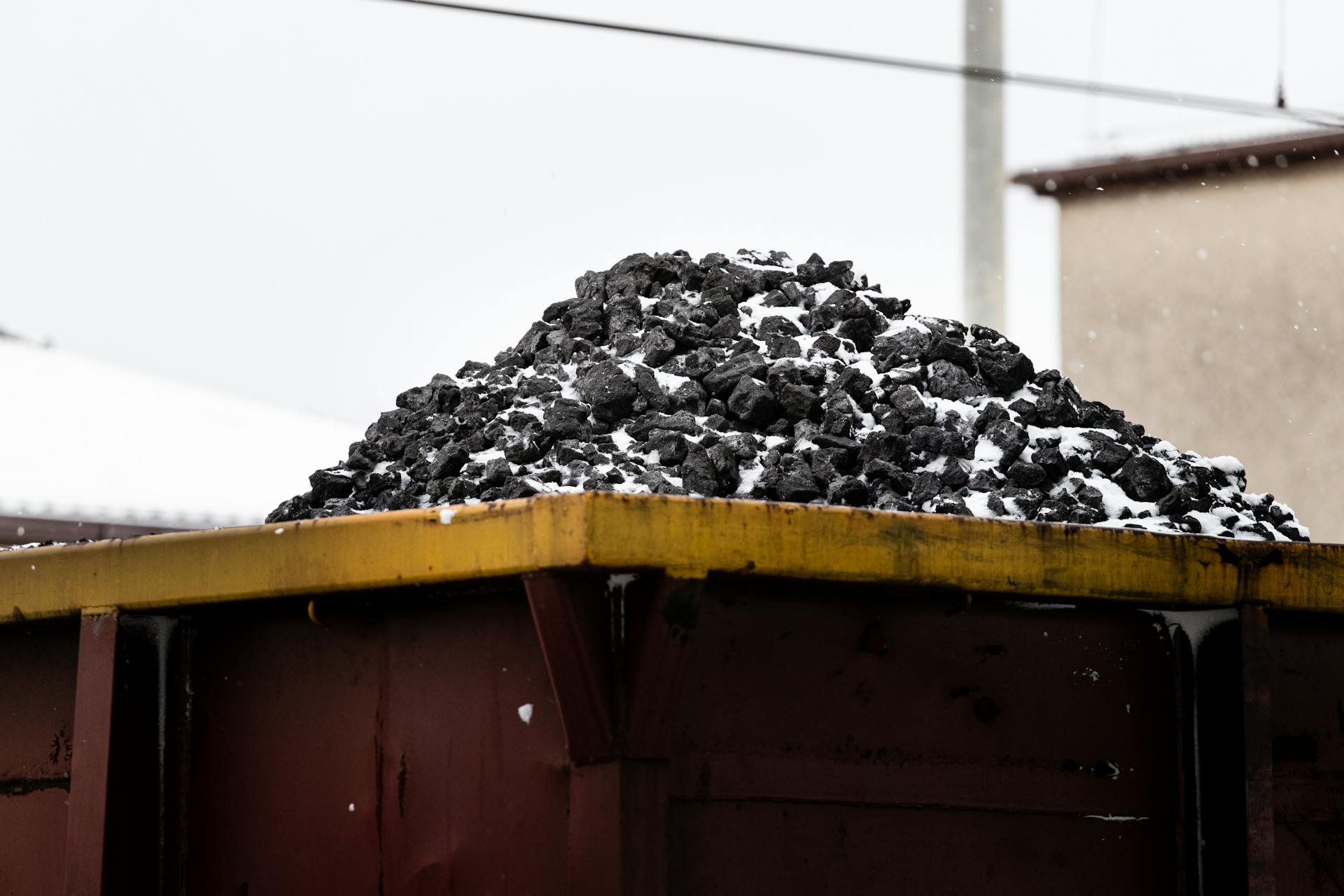
Coal trains are a vital part of the global economy, transporting coal to power plants, industrial facilities, and other destinations. They're a complex operation that requires careful planning and execution.
Coal train carriages are typically made of steel, with a typical length of 50-60 feet and a weight capacity of 100-120 tons. These dimensions allow for efficient transportation of coal while minimizing the risk of derailment.
The operation of coal train carriages involves a series of mechanical and electrical systems that work together to keep the train running smoothly. This includes the braking system, which uses air or electric brakes to slow down the train when needed.
Each coal train carriage is equipped with a unique identification number, which is used to track the carriage's location and maintenance history. This information is crucial for ensuring the carriage's safe operation and extending its lifespan.
Development
The development of coal train carriages involves several key components. The carriages are typically made of steel, which provides a strong and durable material for transporting coal.
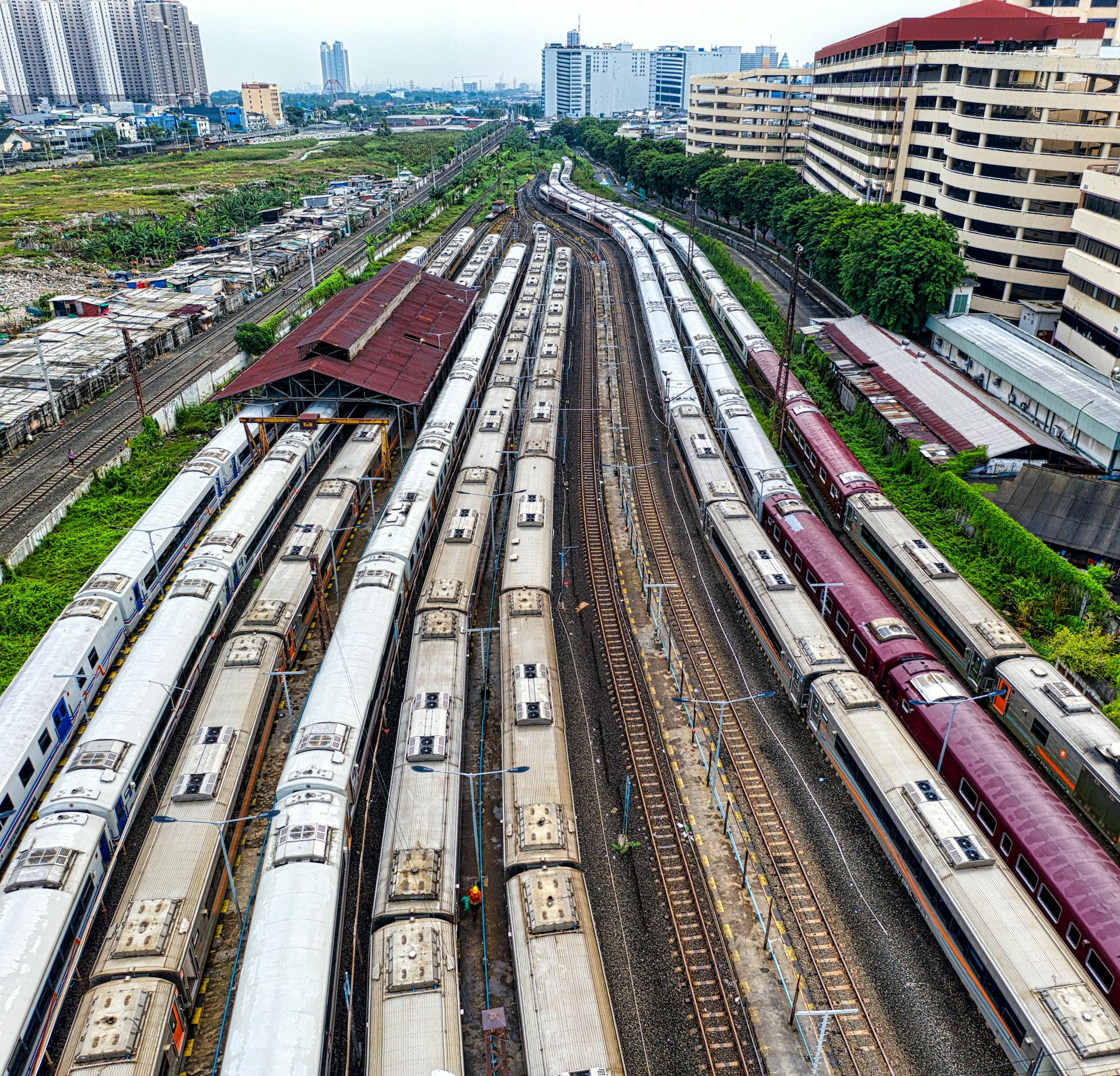
The length of coal train carriages can vary, but they are often around 50-60 feet long. This length allows for efficient loading and unloading of coal at rail yards and ports.
Coal train carriages are designed to carry heavy loads, with some carriages capable of holding up to 100 tons of coal. This is a significant amount of coal, equivalent to the energy needs of a small town for several days.
Design and Manufacturing
Design and Manufacturing is a crucial step in the development process. A well-designed prototype can save time and resources in the manufacturing phase.
The design phase involves creating detailed specifications and blueprints for the product. This includes defining the product's functionality, materials, and dimensions.
Prototyping is a key aspect of design and manufacturing, allowing developers to test and refine their ideas before moving to production. In the article, we saw how a company created a functional prototype of their product in just a few weeks.
Manufacturing involves bringing the design to life, using various techniques such as 3D printing or injection molding. The choice of manufacturing method depends on the product's complexity and the desired level of customization.
The development team should consider factors such as production costs, lead times, and quality control when selecting a manufacturing method. By doing so, they can ensure that their product meets the required standards and is delivered on time.
Testing and Quality Control
Testing and Quality Control is a critical phase of development that ensures the product meets the required standards. This phase involves identifying and fixing defects, as well as verifying that the product works as expected.
Thorough testing helps to reduce the risk of errors and bugs, which can be costly to fix later on. In fact, a study found that it costs 15 times more to fix a bug during the testing phase than it does to fix it during the development phase.
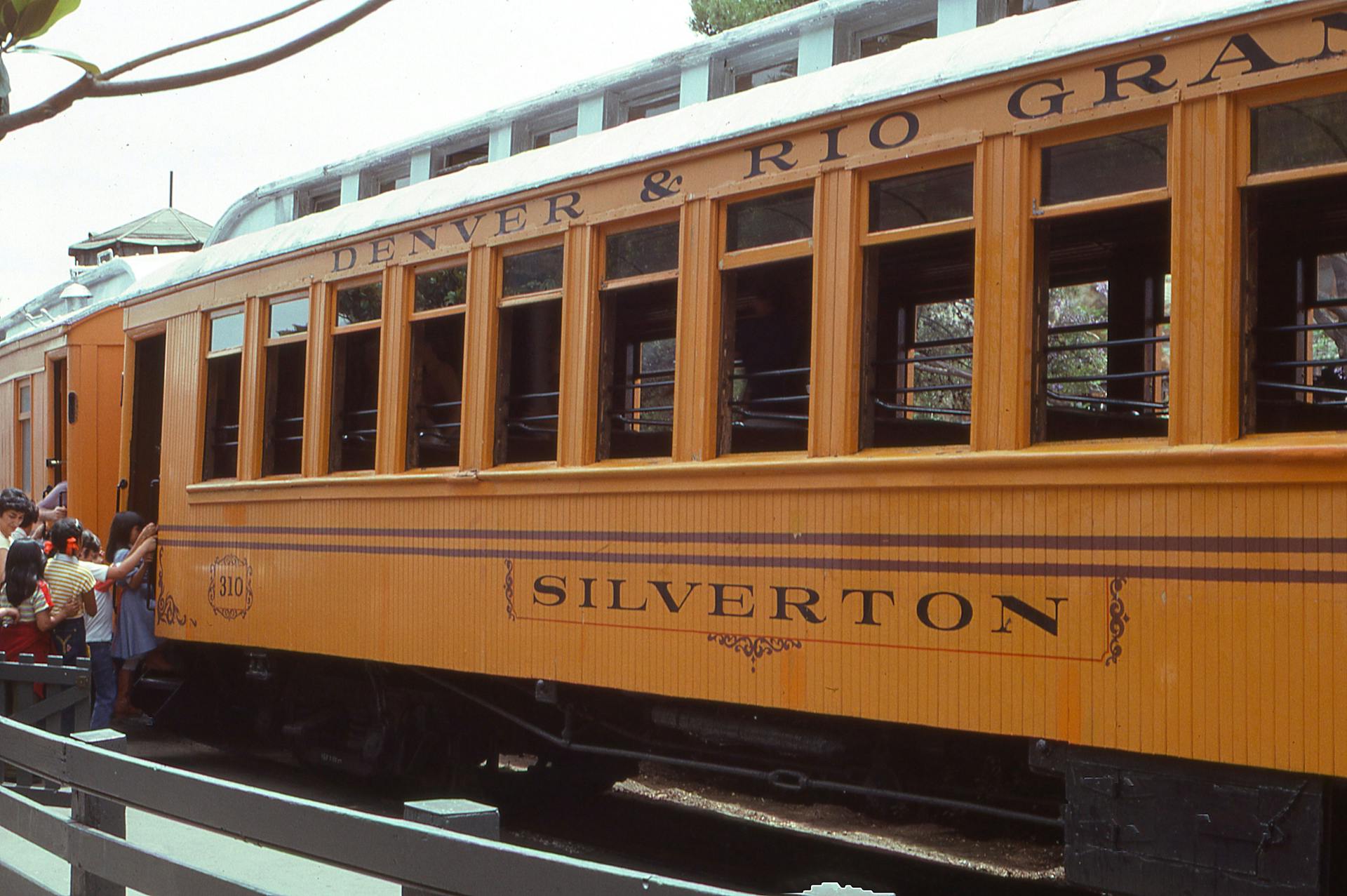
Automated testing tools can be used to streamline the testing process and increase efficiency. For example, unit testing can be used to test individual components of the product, while integration testing can be used to test how these components work together.
A well-planned testing strategy is essential to ensure that all aspects of the product are thoroughly tested. This includes testing for performance, security, and usability.
Coal Train Components
Coal trains are a crucial part of the coal mining process, and they're made up of several key components.
The locomotive is the heart of the coal train, responsible for hauling the train and its cargo.
The coal train's propulsion system is typically diesel-electric, with a diesel engine driving an electric generator to power the locomotive's electric motors.
The train's brake system is designed to slow and stop the train safely, with air brakes being the most common type used in coal trains.
Expand your knowledge: Australian Tractor Trailer Trains
Coal cars are the containers that hold the coal, and they're designed to be strong and durable to withstand the weight and rough handling of the coal.
The coal train's control system allows the engineer to control the train's speed, direction, and braking, and is typically operated from the locomotive's cab.
Operations
A coal train carriage is a self-propelled or unpowered vehicle designed to transport coal from one place to another.
The length of a coal train carriage can vary, but it's typically between 20 and 30 meters long.
Coal train carriages are designed to carry heavy loads, with some models able to hold up to 80 tons of coal.
In addition to carrying coal, some coal train carriages also have the ability to carry other materials, such as sand or gravel.
Maintenance and Repair
Regular maintenance is key to keeping operations running smoothly. In fact, a study found that a 1% decrease in maintenance costs can lead to a 2% increase in productivity.
Equipment downtime can be costly, with some machines costing upwards of $10,000 per hour to repair. This is why it's essential to schedule regular maintenance checks to catch potential issues before they become major problems.
Routine inspections can help identify worn-out parts and prevent costly repairs. For example, replacing worn-out bearings on a machine can cost as little as $100, compared to the $10,000 it would cost to repair the machine if it were to break down completely.
A well-maintained machine can last up to 20% longer than one that is not properly maintained. This is because regular maintenance helps to prevent wear and tear on parts, reducing the need for costly repairs and replacements.
In some cases, maintenance can even be done on the fly, with some machines allowing for quick and easy repairs in the field. This can save time and money by reducing the need for specialized tools and equipment.
By prioritizing maintenance and repair, operations can run more efficiently and effectively, leading to increased productivity and reduced costs.
Safety Protocols
Safety Protocols are in place to protect staff and visitors.
The facility has a comprehensive emergency response plan that includes evacuation routes and assembly points.
Regular fire drills are conducted to ensure everyone knows what to do in case of a fire.
The facility's emergency phone system is tested monthly to ensure it's working properly.
Staff are trained to respond to medical emergencies, including first aid and CPR.
The facility has a policy of reporting all incidents, no matter how minor they may seem.
First aid kits are located throughout the facility, easily accessible to everyone.
Expand your knowledge: Conex Container Fire Training
BNSF Requirements
The BNSF has strict regulations for coal car dust control, and Midwest's Coal Car-Topping System meets these requirements.
To comply with BNSF regulations, you need a reliable and consistent dust-control sealant for coal in transport.
Soil-Sement Engineered Formula CCT has been tested and verified by Simpson Weather Associates Laboratory for weatherability, and by BNSF for corrosion, safety, and performance.
Related reading: Bnsf Coal Train Derailment
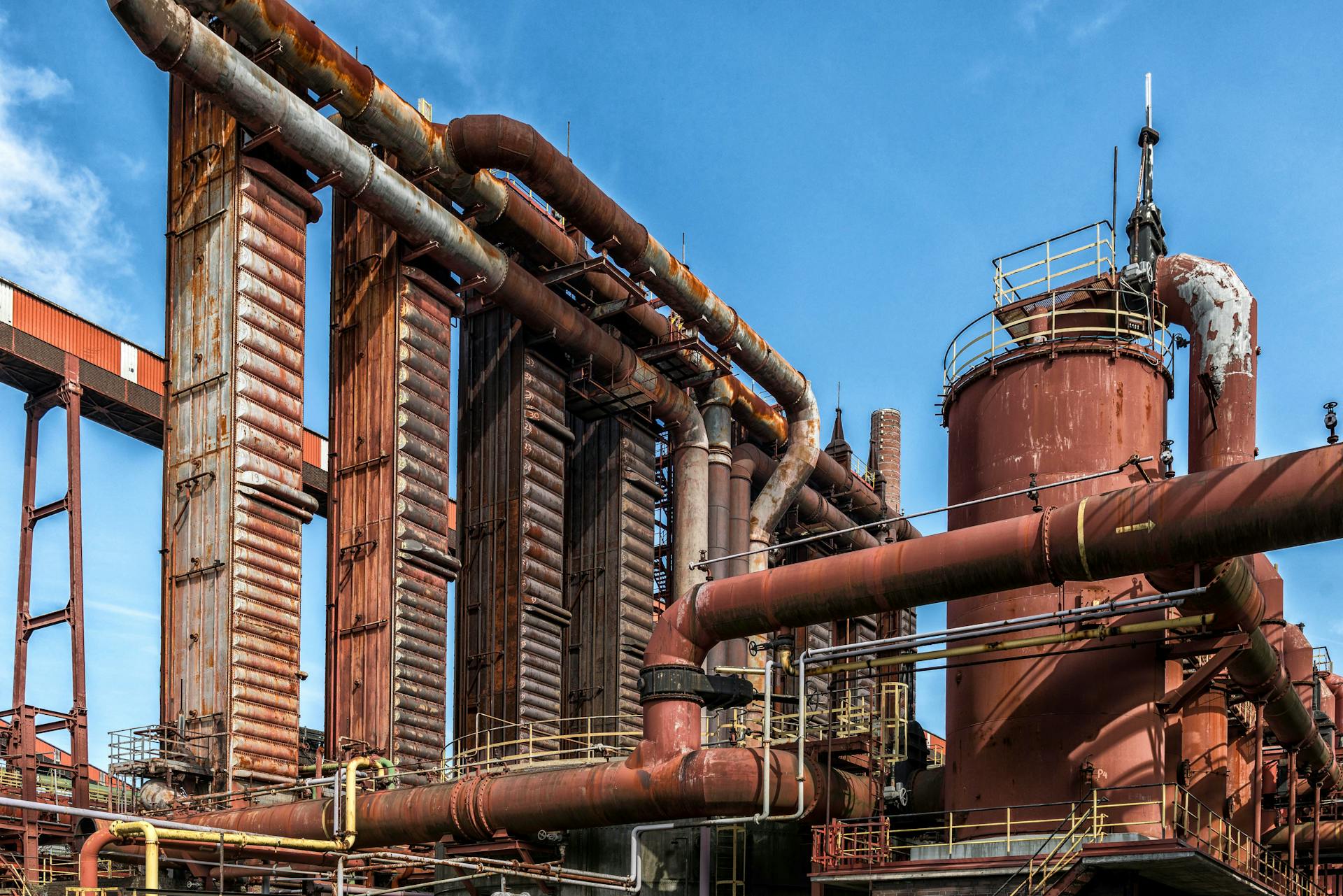
This formula delivers peace of mind, as it has proven to be the most reliable and consistent dust-control sealant for coal in transport.
Midwest is one of less than a handful of approved BNSF vendors, which means their system has met the BNSF's high standards.
- BNSF approved vendors like Midwest have met the BNSF's high standards for coal car dust control.
- Soil-Sement Engineered Formula CCT has been tested and verified by BNSF for corrosion, safety, and performance.
Regulatory Compliance
Regulatory Compliance is a top priority for coal train carriages. As mentioned in the article, coal dust is a health hazard and creates an environmental hazard for which railroad, utility, and mine management will be held responsible.
Midwest's Coal Car-Topping System is a year-round solution that meets BNSF and regulatory requirements. This system is designed to eliminate dust from in-transit operations.
To ensure compliance, Midwest's Soil-Sement Engineered Formula CCT has been tested and verified by various organizations, including Simpson Weather Associates Laboratory, BNSF, and Southern Company. It has proven to be the most reliable and consistent dust-control sealant for coal in transport.
The system is also durable enough to spray 24/7, 365 days a year, and permanently installs over railcars. This makes it easy to apply the dust suppressant, Soil-Sement Engineered Formula CCT.
Here are some key features of the Coal Car-Topping System:
- Protects against freezing with a heated container
- Allows a clear view of coal cars from a heated, raised operator’s booth
- Adjusts to match the profile of coal in a railcar
- Durable enough to spray 24/7, 365 days a year Installs permanently
Frequently Asked Questions
What is a coal wagon called?
A coal wagon is also known as a mineral wagon or coal truck. It's a small, open-topped goods wagon used to transport coal and other products from mines.
How much coal fits in a train carriage?
A typical coal railcar can carry 100 to 110 tons of coal, with some cars holding up to 125 tons.
Sources
Featured Images: pexels.com